Ceramic Bearings vs Steel Bearings: An Engineering Analysis
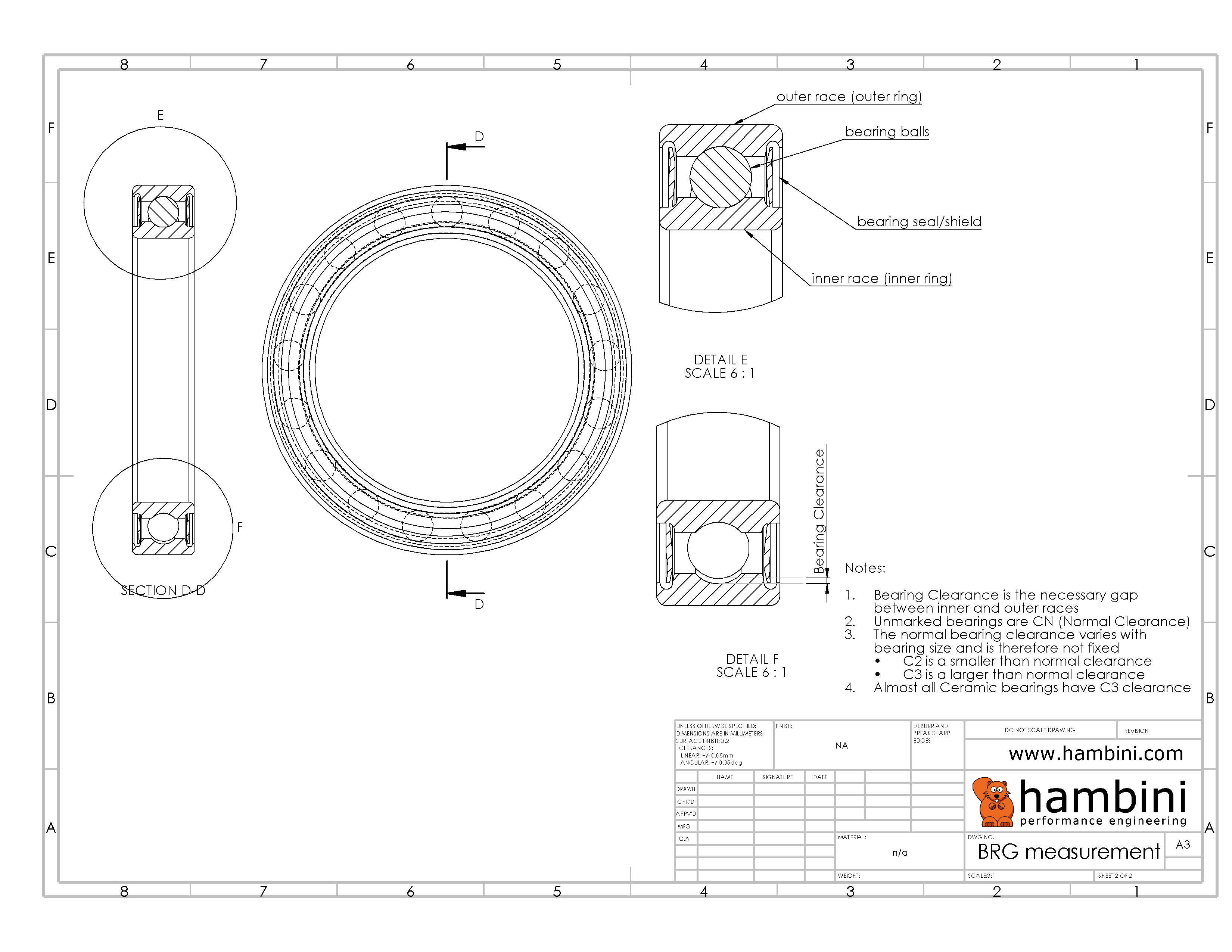
One of the most controversial topics in the cycling industry is with regards the topic of Ceramic bearings and whether they do or do not reduce friction dramatically in riding. This article will address some of the concerns and topics associated with this debate and quantify the numbers.
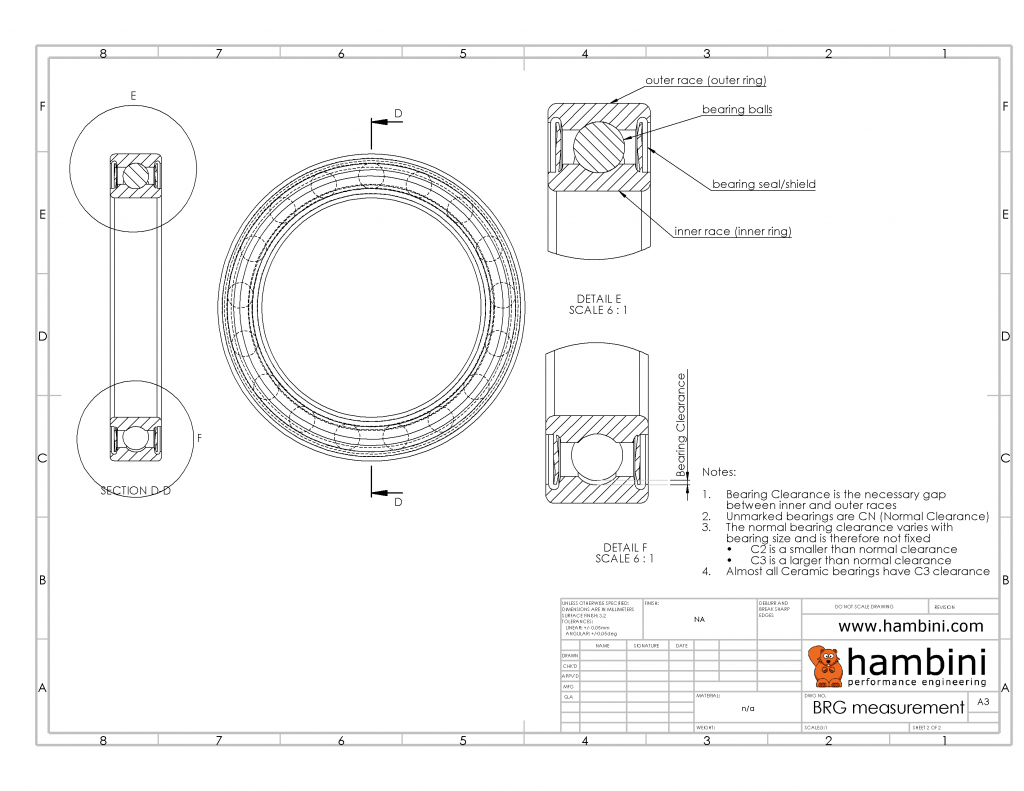
Internal Bearing construction – Ceramic bearings are not 100% ceramic
Ceramic bearings are in actual fact hybrid. They use ceramic balls and usually a steel inner and outer race. The ceramic balls are often silicon nitride or equivalent. Steel Bearings are commodity items that are composed of hardened steel balls and a steel inner and outer race. Geometrically, the contact points, inner and outer dimensions and thickness between steel and ceramic bearings is the same so they are interchangeable. The only real big noticeable difference between the two is the bearing clearance. On ceramic bearings, this is usually a C3 clearance whilst on steel it’s usually CN.
The bearing clearance is a measurement given to the small gap between the inner race, outer race and balls. It is required to prevent bearing seizure when it warms up and expands.
Another common difference in bearing construction is the cage type. The cage is required to keep the ball spacing even all of the way around the bearing. On steel bearings (usually by Japanese manufacturers NSK, NTN) the cage is a ribbon that is made from a piece of pressed metal and riveted between balls. This is a comparatively costly method of construction but improves friction characteristics at low speed and stiffness.
An alternative method of cage construction that has become popular is a composite or rubber cage. This cage snaps in and holds the ball spacing. Under high loads, the cage can often pop off or deforms and causes more friction. Almost all ceramic bearings use a composite or rubber cage.
External Bearing Construction – the Seals
Bearing seals come in 4 generic types. There are open bearings – these have no seals, metal shielded bearings – these have a metal strip over the bearing cage, non contact seal bearings and fully contacting sealed bearings.
In the bicycle industry, bearings generally have non contact or fully contacting seals. This is in light of the real risk of contamination from dirt and other ingress. In theory, non contacting seal will have the same friction level as a completely open unsealed bearing, in practice this is not quite the case because the seals generate a barrier for lubricant to ride up against and this is a frictional loss. Fully contacting seals touch both the inner and outer races to maintain the seal. This is definite frictional loss and they will always appear to be draggy when rotated in the hand. At operating speeds this loss from friction is still there but not so noticeable.
Basic bearing seal technology has not changed dramatically since the sixties and is largely governed by manufacturing costs rather than performance. Over time, the main improvements have come from sealing materials rather than geometrical differences.
Bearing Production
Bearing production in volumes is an almost entirely automated process and was pioneered by the Japanese. The big four (SKF, NTN, NSK and FAG) produce thousands of bearings every second with little human intervention. The bearings are usually made on one site from raw material to boxed finished product. These bearings are almost always steel.
In contrast, the smaller ceramic suppliers (Enduro, Kogel, Ceramicspeed) have much more human intervention and often complete assembly of bearings by hand. The smaller companies do not have the ability to carry out the entire manufacturing process on site and typically subcontract the manufacturer of one or more parts of the bearing to a third party and then complete the final assembly in house.
Some suppliers of ceramic bearings buy in a generic hybrid assembly and laser etch their own brand name onto the side of the bearing. These bearings are purchased at very low sums ($5/£5/€5) from the far east and then sold on for 10 or even 20 times the price to consumers in the US and Europe. It’s easy to spot these manufacturers as they are usually sold by one supplier only and lack technical data.
Bearing Friction
The large manufacturers have lots of people working specifically in their engineering departments whom end users can consult for technical advice.SKF, NTN, NSK and Schaeffler (FAG/INA) provided the graphs shown below which show the proportion of frictional loss for each component of a bearing.
Whilst the proportion of friction associated to each component of a bearing varies slightly, the overall values and order are the same. The bearing seal is the biggest loss, followed by the lubricant. The rolling friction is extremely small.
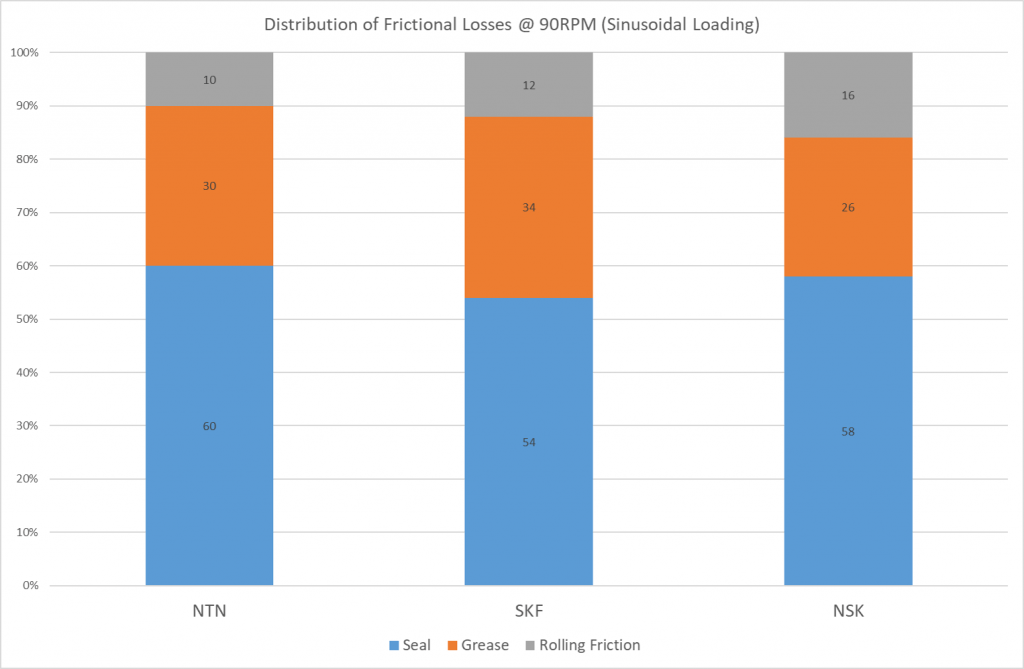
Schaeffler (FAG/INA) went a stage further and gave the breakdown into the constituent components
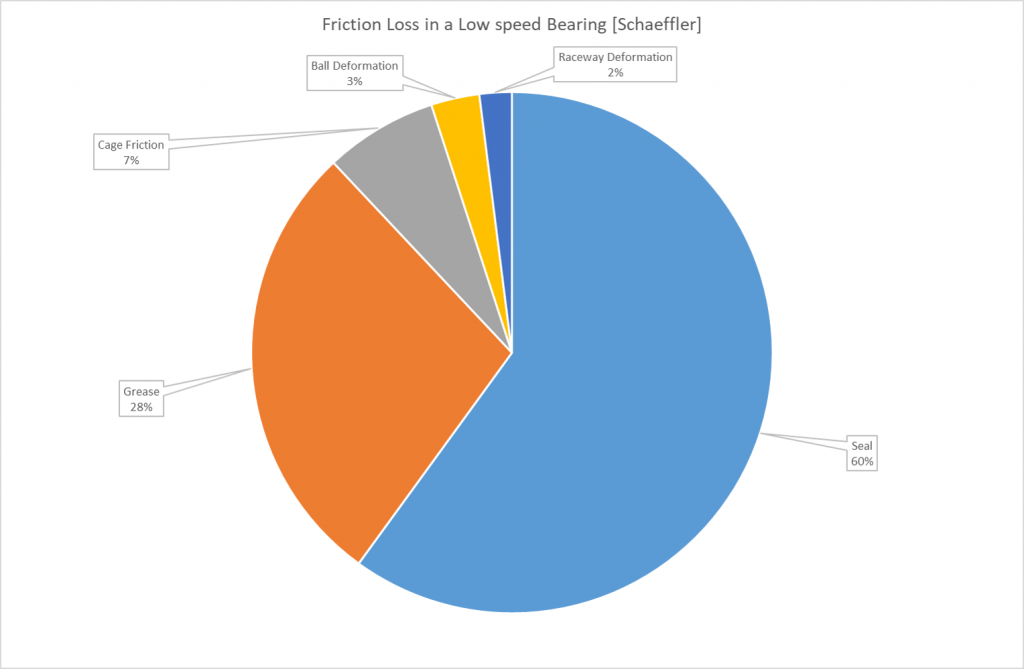
Schaeffler’s data is useful because it shows how small the potential gain by switching from steel to ceramic bearings is. The maximum improvement is a potential 3%. In practice, rolling friction cannot be eliminated so the likely figure is more like 10% of the 3% ie 0.3%.
The cage friction is worthy of attention because ceramic bearings almost always have snap in cages. These have consistently been shown to have more friction than pressed metal cages. So whilst ceramic bearings could reduce the rolling friction (3%), they will inevitably increase the cage friction (7%). The net result is a steel bearing will have lower friction.
To illustrate this practically, a small experiment was carried out to neutralize the effects of grease and seals. Two bearings, an Enduro ceramic and an NTN LLB (Non Contact) steel bearing had their power loss measured at different stages of disassembly. The graph below shows the process
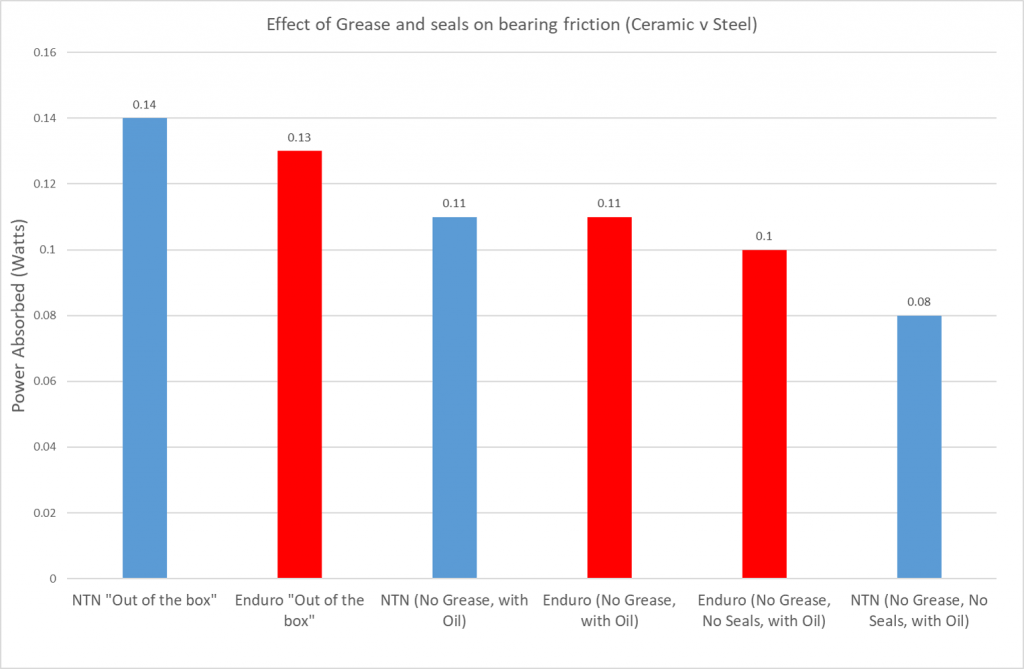
There are three states. The first is out of the box. The second is the removal of grease and replacement with oil. The third is removal of grease, replacement of oil and removal of seals.
In out of the box configuration, the Enduro bearing has fractionally lower power loss. Once the grease has been removed, the power loss of both bearings is equal. After the seals have been removed, the NTN bearing has comfortably lower friction. This correlates well with the data provided by NTN, NSK, SKF and Schaeffler.
Bearing Friction vs Life
An often neglected part of tribology is how a bearing responds as it wears out. The graph below shows a comparison between two steel bearings (SKF and NTN) and a Ceramic bearing (Enduro). Initially the Enduro bearing has lower friction, at around 600km of use, the ceramic bearing has worn a track into the comparatively soft steel races and the bearing friction starts to increase dramatically. It is comfortably higher than steel bearings after a modest running in period. Hybrid ceramic bearings are the equivalent of trying to run a locomotive on an asphalt road – the hardness differential causes the road (raceway) to become damaged.
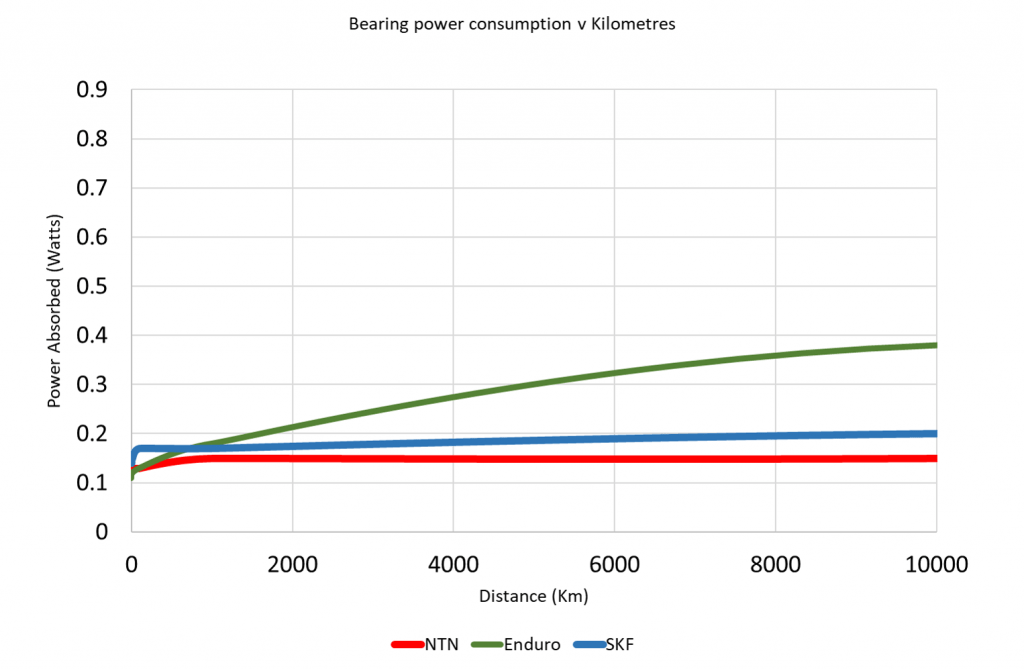
Total Power saving
The graph below shows how much power could be saved over 1000km between different bearing brands and their seal types. NTN, NSK and SKF dominate this chart and that is largely due to efficient seals and metal cages. The ceramic bearings which are coloured in red are not quite as efficient over a prolonged distance. If the evaluation window was extended to 10,000km, the ceramic bearings would perform much worse as a more significant track would have worn into the bearing races thereby increasing friction.
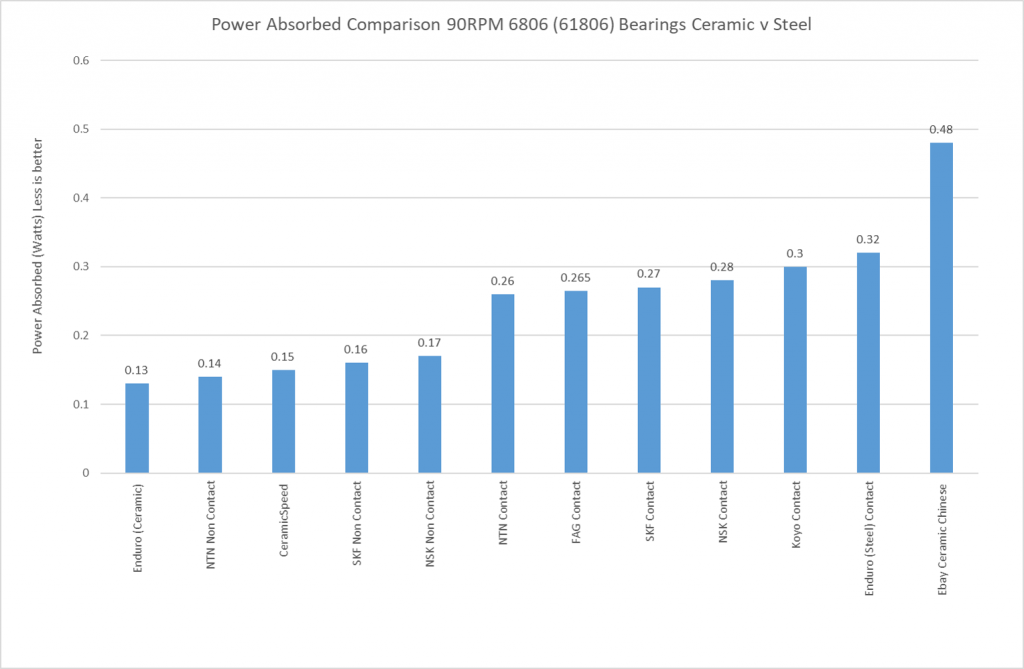
Watch the Video!!
You can see a bit more of the bearing internals in this video I have made
Dear Hambini,
Like you I got the winspace hyper wheelset, 50mm rim brake. BUT they only come with ceramic bearings! Can you give me the part number for the NTN bearing that would fit the hyper hub? And is it difficult to replace the bearings?
6803 x 5 ( 2 for the freehub, 1 for the rear hub and 2 for the front wheel), 6903 x 1 for the rear hub.
Following your recent teardown of the Hypers, it sounds like this is amended to 5x 6803, 1x 6903 (rear hub drive side)? I expect the same configuration applies regardless of depth/brake system. I have a set of 50mm disc that I’ll be pulling apart shortly to confirm…
For those interested in watching a 5yo gracefully disassemble and reassemble the aforementioned: https://www.youtube.com/watch?v=vdHhfcU_wmw&t=1298s&ab_channel=Hambini
That’s interesting. I just been in contact with Winspace and they sent me details saying it’s still 4×6803 and 2×6903 for the Hyper 50s.
Disregard, I was reading it wrong. The set does have 5 x 6803 and 1 x 6903
Interesting to compare the NTN data on distribution of friction losses attributing 60% of losses to the seals, but only a 43% reduction in losses when both removing the seals and replacing the grease with oil.
What is the source of the bearing power consumption vs km graph?
Yap thats really fascinating…
It is 60% accounting for the seal and 30% of total for the grease out of the box for the NTN according to the provided data.
But then removing the seal completely and the grease and only use oil only saves 43%…
Something’s appears wrong here. The saving should be higher than that… at least -60% for removing the seal and some more percent for oil instead of grease!
When the NTN LLB is stated to have only 10% friction by material itself… it must save more than 50% removing the seals and replacing, and heres the problem i found it.
The initial picture (60% for seals) shows the standard bearing of NTN (contacting seals) but the graph with the savings from removing seals and oil is for the LLB-bearings of NTN… of cause that one has lower friction for the deals initially!
Everything is correct! The first picture is NOT for LLB! LLB has quite lower friction than 60% for the seals… i think around 20-40% and therefore around 50% for the grease, so for that it fits perfectly with the savings with removing seals and using oil!
You missed that point!
See the total friction of the LLB is lower but in percentage it is diffeerent than the first picture shows with the “standard” of the manufacturers
Instead of the seals having the highest friction, it now becomes the grease, with the LLB-version … surely!
I assume – of that lower total – around 13-15% Material, 22-30% Seals and biggest part now having the Grease with 55-65%.
Even if you remove that ~25% of the Seal (-25%) and replace that ~60% with oil down to 42% (-18%)… thats only -43%.
Thats it!
So 60% for the seals is for standard “contacting” seals…. if you remove the seals on them and replace the grease with oil on them that saving is indeed higher than the 43% shown for the LLB of NTN!
That minus 43% through removing seals and replacing grease with oil is only for the NTN LLB which has very little for the seals at all!
In total still the NTN LLB with or without seals with grease or with oil going to have less friction than the standard whatsoevever. Only your percentage-wise win on the standard is higher doint the tuning… but in total the LLB always going to be better in comparison, whatever you do!
What about rust and seizure in extreme conditions? Wouldn’t a ceramic bearing far outperform a steel one? And how differently contaminants ingress affect the lifespan?
All bearings have steel races, so the ceramic isn’t going to win in that regard. Your question is really around which seal type is better and for inclement weather, you are better off with full contact seals.
Full ceramic bearings do exist.
Ceramic races are too brittle for use in most cycling applications, and are liable to fail due to shock loading. A failure of a wheel bearing at high speed would be catastrophic.
This analysis only applies to cycling applications?
Is “total power saving “chart numbers applies per 1 wheel or wheelset?
it’s per wheelset
From SKF:
“Because of the properties of ceramics, a hybrid bearing’s service life can be up to 10 times that of a standard steel bearing, reducing the need for maintenance on your machine as well as the costly interruptions in production.”
How do ceramic hybrid bearings claim to have a longer service life if the friction surpasses that of all metal constructions so quickly? Would this increases friction not cause accelerated wear?
In a pure running machine that is not subjected to road vibration this statement is probably valid. As soon as the external vibration is added, the advantage is negated.
You mention some smaller companies like Enduro etc here, but what are your thoughts on Chris King bearings (in general, ie, their both their steel and ceramic) compared to SKF/NTN/NSK/FAG etc?
They are such a niche product that there isn’t as big of a sample size.
I’m sorta persuaded, but have questions: 1) Does the initially lower power consumption for the Enduro Ceramic bearings show that their seals are more efficient? 2) what’s the source of the data in the “Bearing Power vs. Life” chart? Your own testing? Published data? 3) the last chart is not what’s described in the text.
I’m wanting to get some better bearings for a wheelset I want to buy and the manufacturer says that the front hub uses 2 x 18307 bearings. I was hoping for NTN bearings but not able to find this size bearing on the bearing websites. Is there an equivalent size? Any advice?
They are available here 18307 Bearing It’s not an ISO size so the options are limited.
Can you factor in a full ceramic full compliment bearing such as what is offered at ORTEC. This could be the ceramic extreme to which a full comparison could be made.