New Bike Frame: Corroding after 2 Months | COTIC
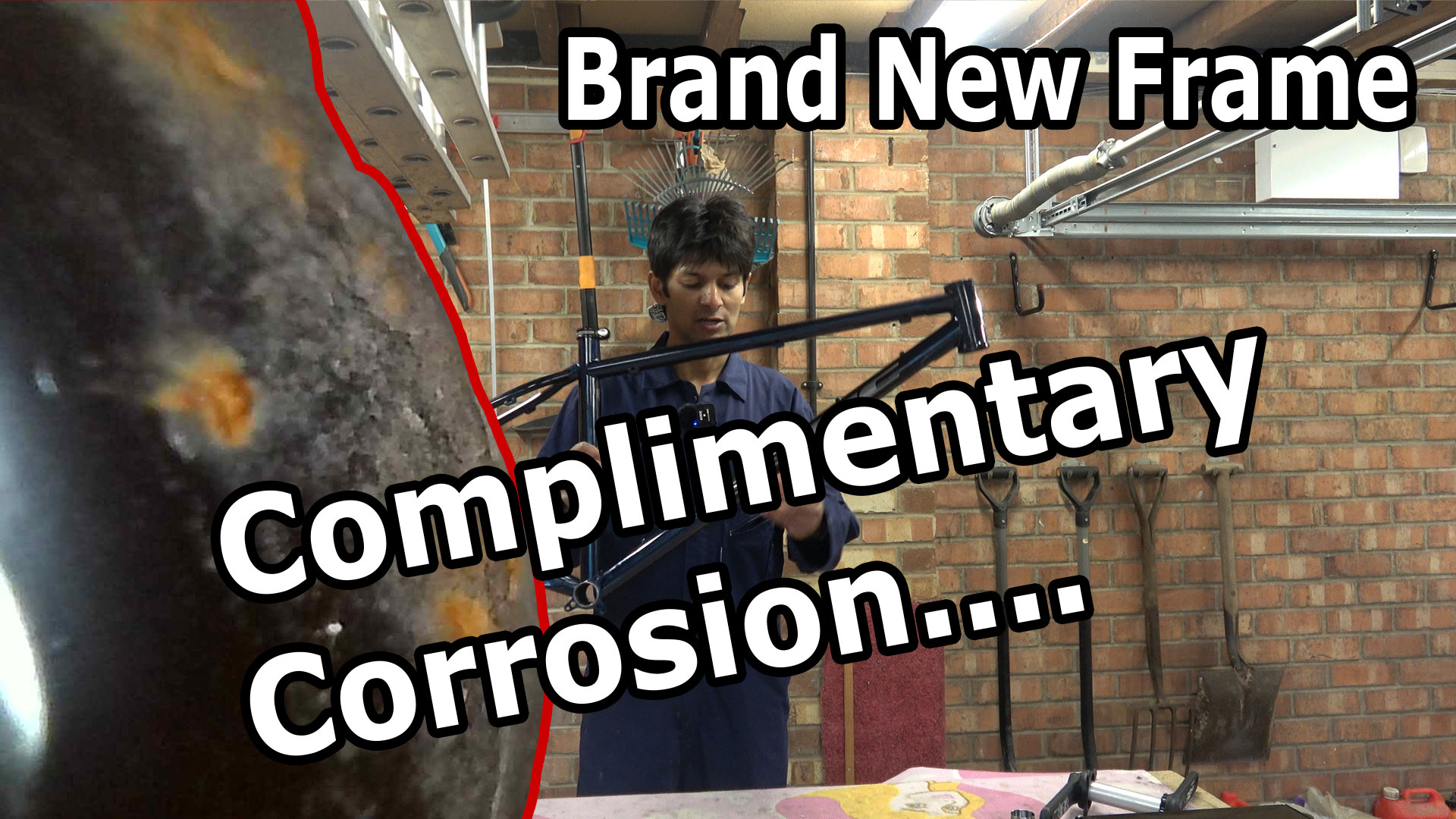
Introduction
A viewer of the Hambini Channel sent in their brand new Cotic Solaris bike frame for a review and a brand new bottom bracket. The frame was a steel mountain bike frame from the British brand Cotic, based just outside of Sheffield, England. The frame was made in Taiwan.
Background
The frame was of steel construction with butted tubing to make up the double triangles, the joints appeared to be welded. The loaded sections such as the bottom bracket and the headtube were of much thicker material. The bottom bracket was BSA and it was required to locate a Rotor Q ring oval crankset. Cotic’s marketing implies this bike is of their own design and specification but a cursory glance at the box suggests this may be an “open mould” or “catalogue” frame that has been rebranded.
Geometrical Checks, Fit and Finish
Geometrically this bike had very good final positions of the interface points. There was very little to fault with the quality of the visible welding and the final finish of the bike. The mounds had all been faced and were square. The bottom bracket had been faced post-painting, it was square and the threads had been chased. The headset bearing locations had acceptable levels of total eccentricity and the shared axis of the upper and lower headset bearings were within reasonable engineering tolerance.
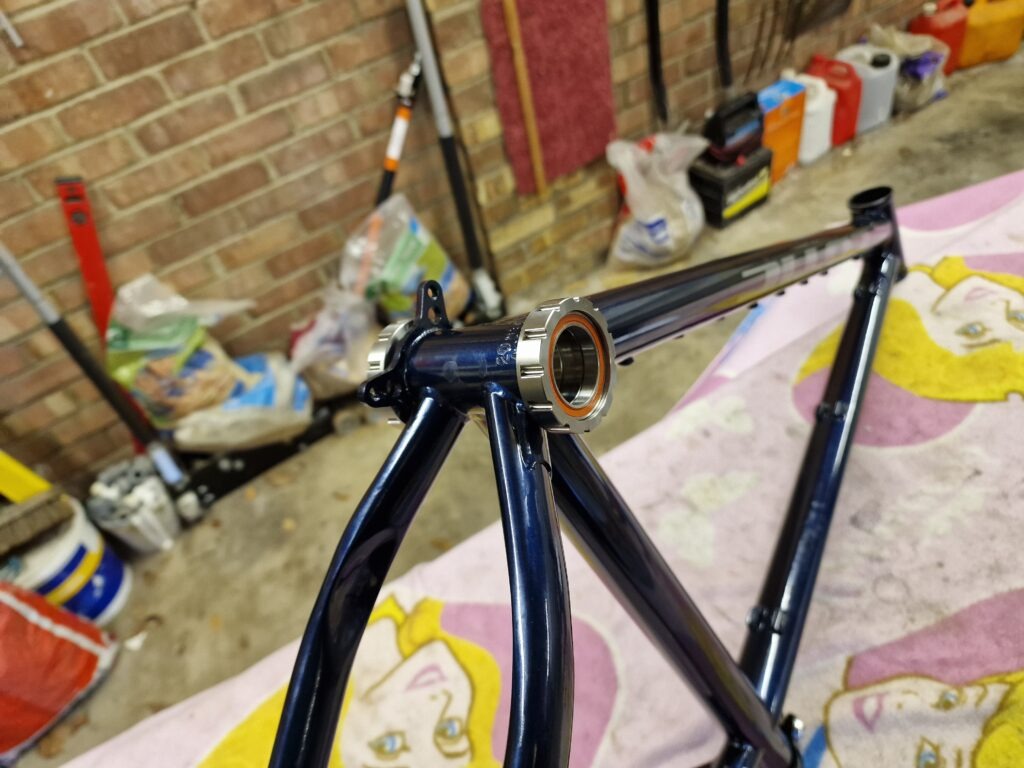
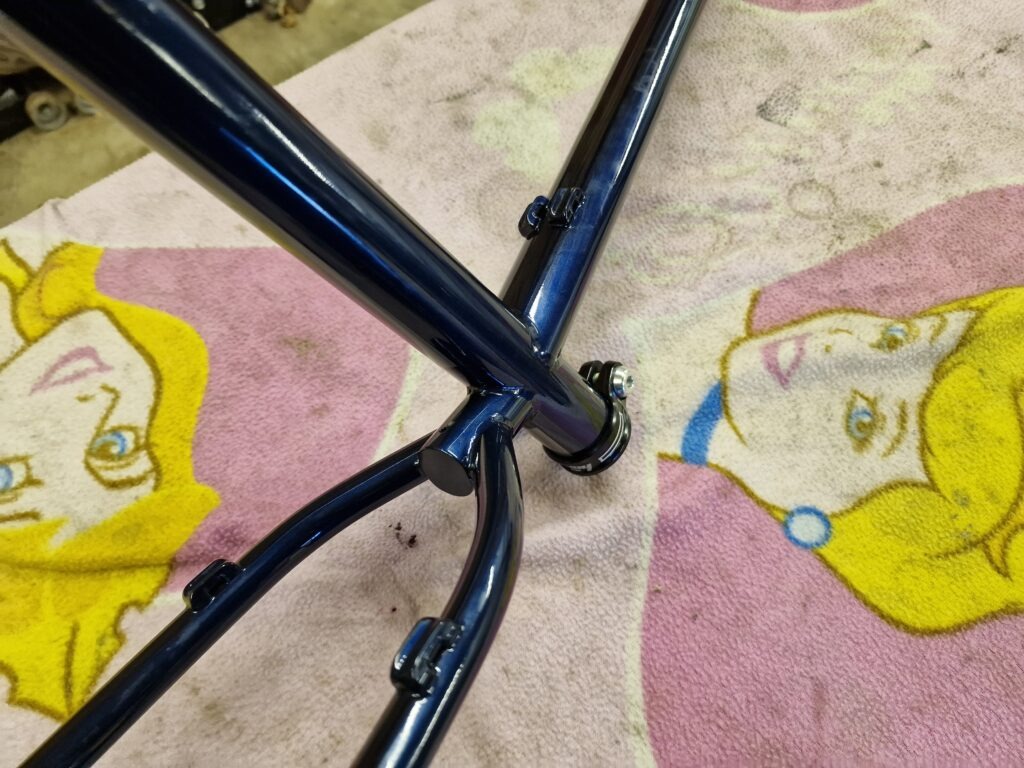
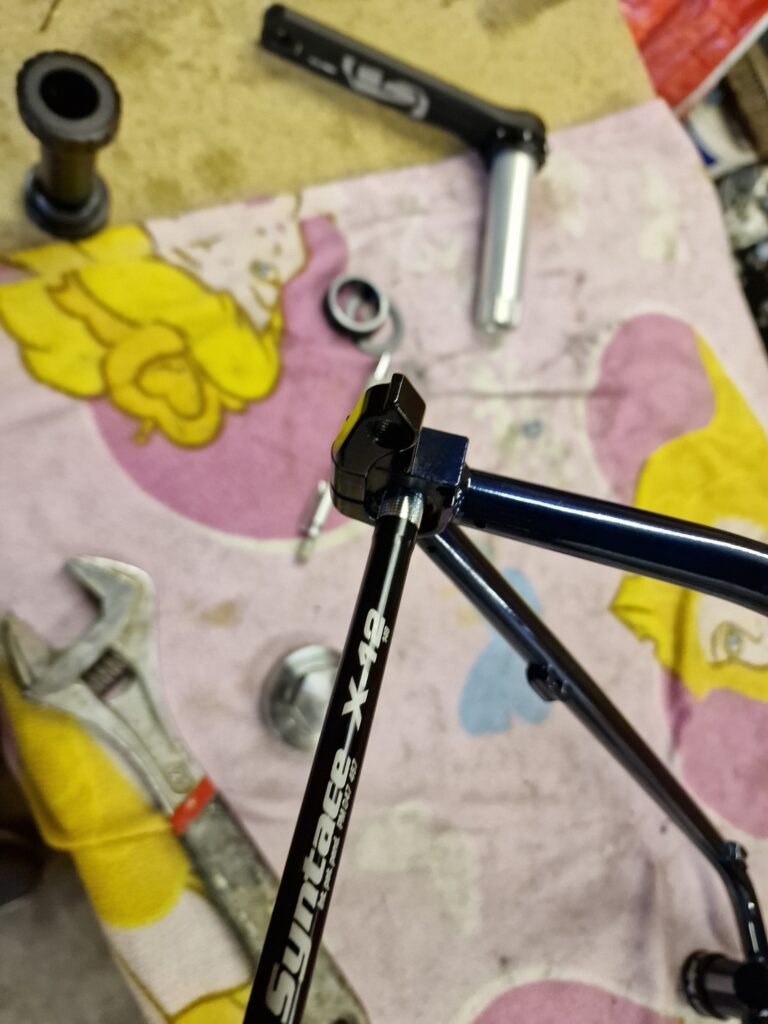
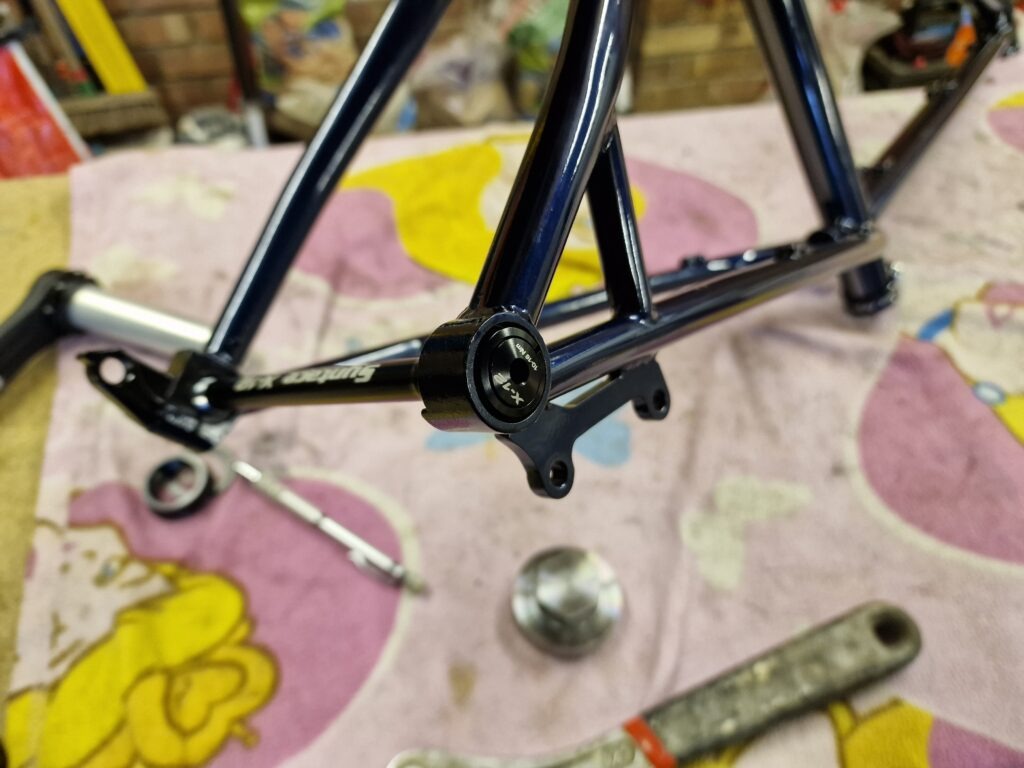

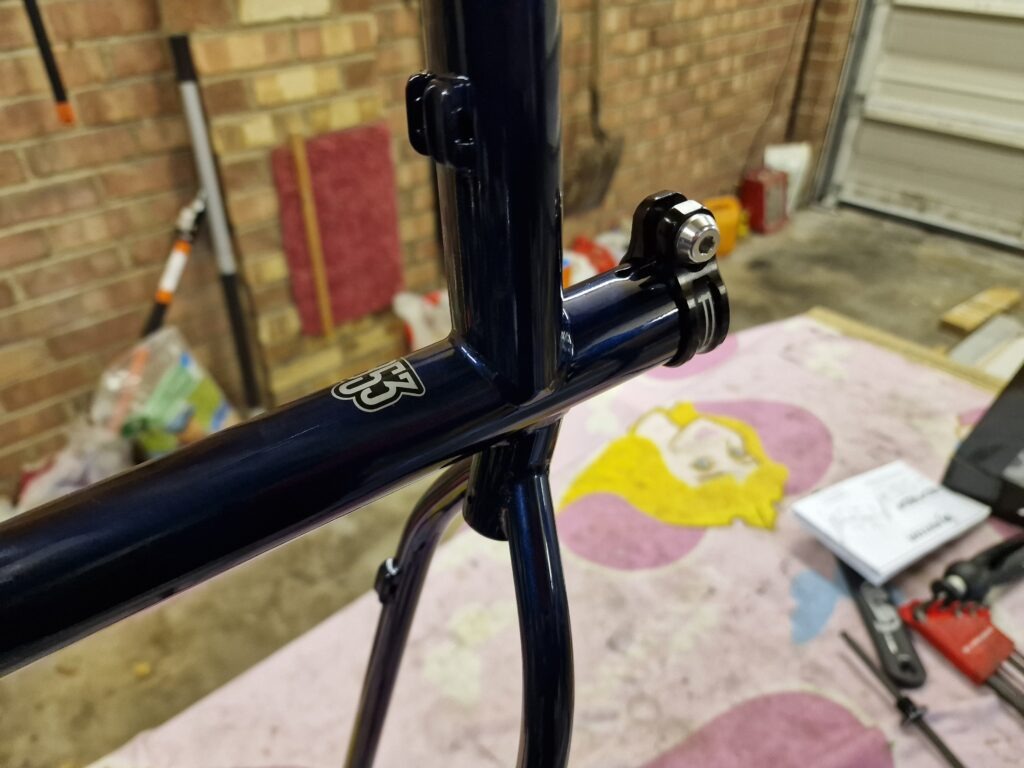
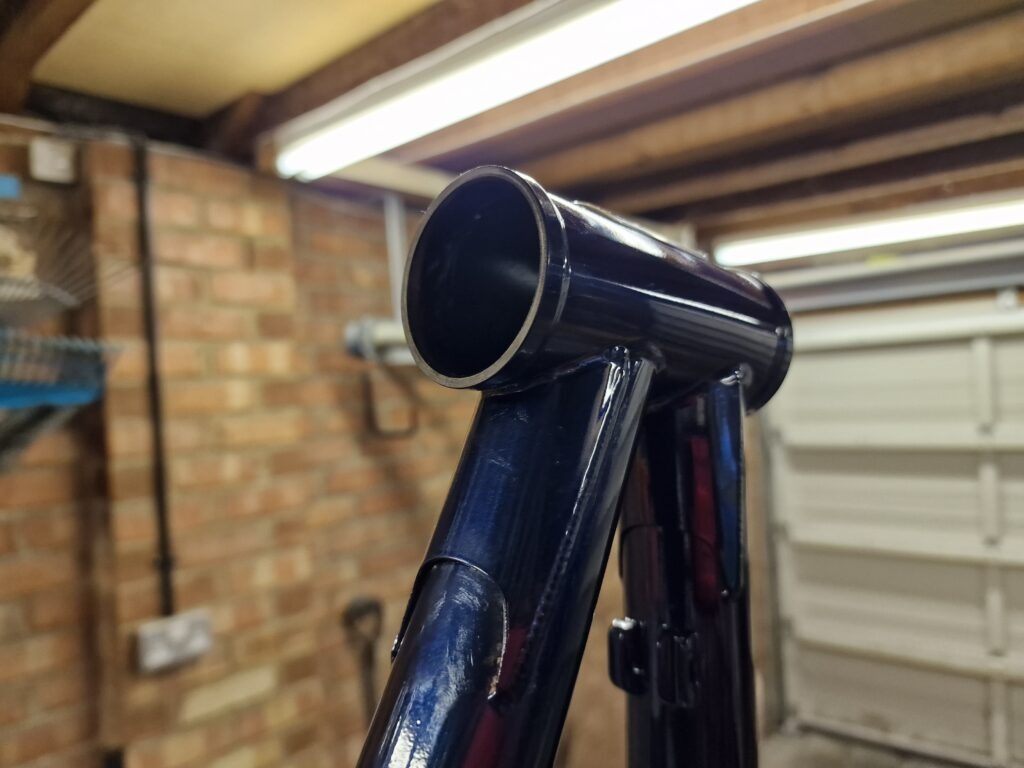
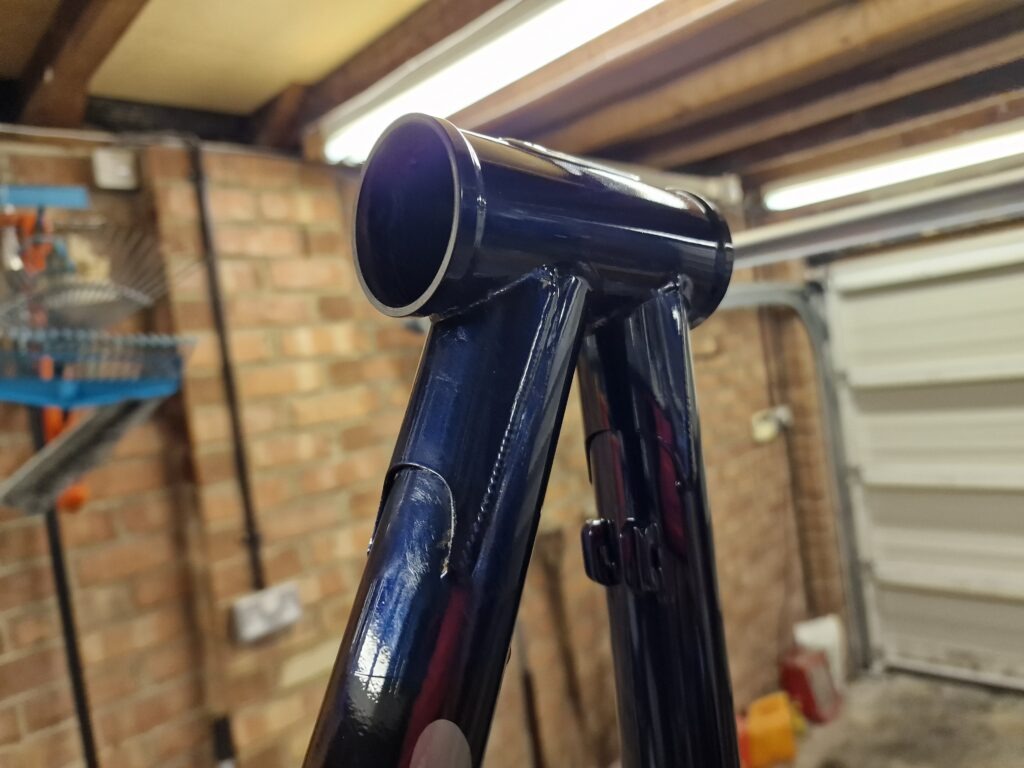
Internal Checks
The frame was inspected internally with a borescope. Access was limited due to small intermediate vent holes between the welded tubes. The inspection revealed the onset of corrosion in structural areas, predominantly around the seat tube intersection, stays and bottom bracket. The visual inspection identified areas of corrosion scale inside the frame. Given the frame was only 2 months old and was claimed to have been zinc phosphate dipped to prevent corrosion it was disappointing.
The corrosion appeared to have preferentially attacked the weld filler and the thicker bottom bracket section. Cotic have claimed the frame is of uniform material despite some of the tubing being of a clearly different colour.
It’s unlikely the frame would fail in the short term but corrosion of this nature – internal, does present some wider problems, the primary concern is the lack of visibility.
The intersection of the bottom bracket, seat tube and stays is ideally suited to detritus, moisture and salt build-up. Combined with poor drainage, this location would be ideal for the corrosion of the joint.
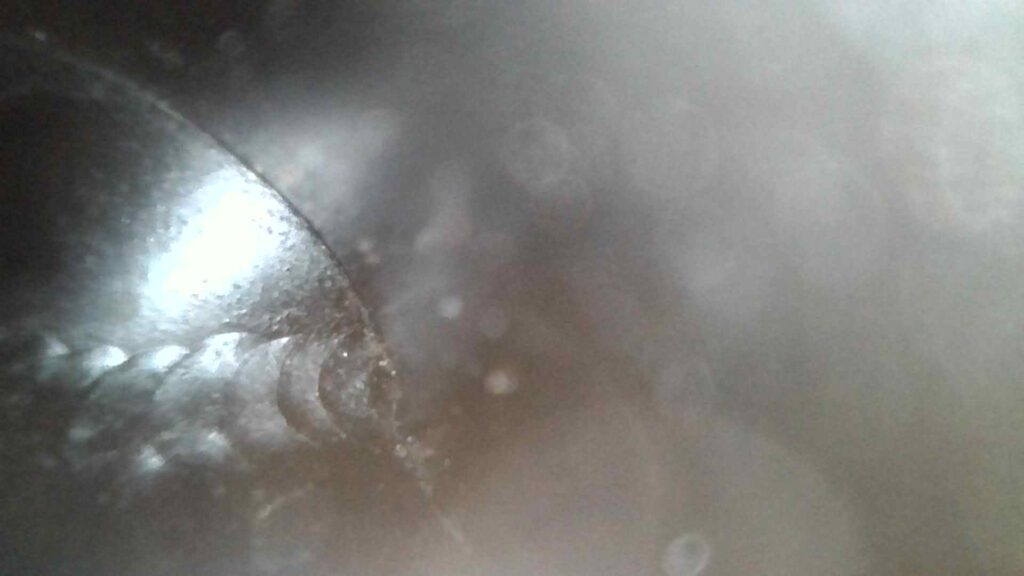
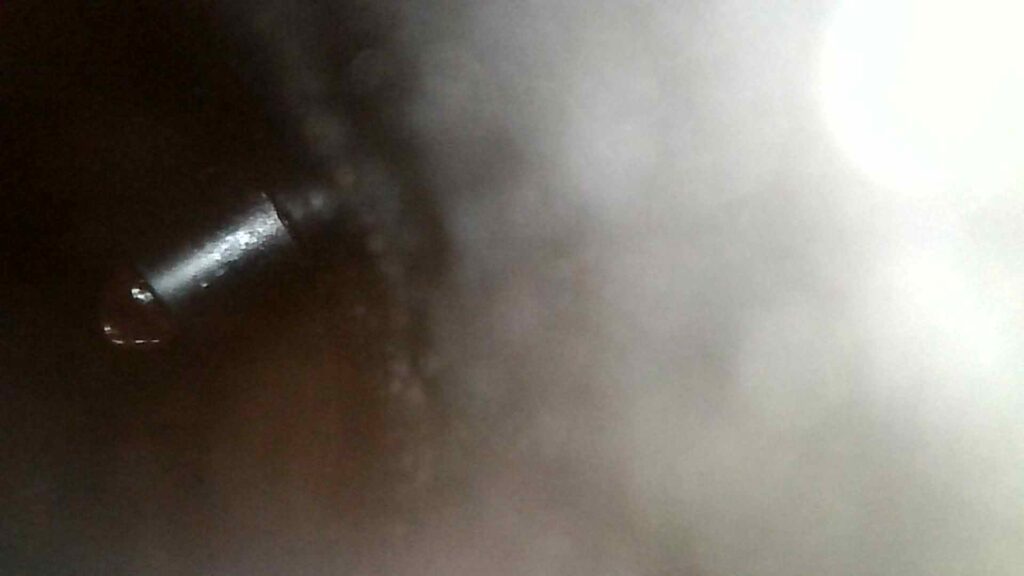
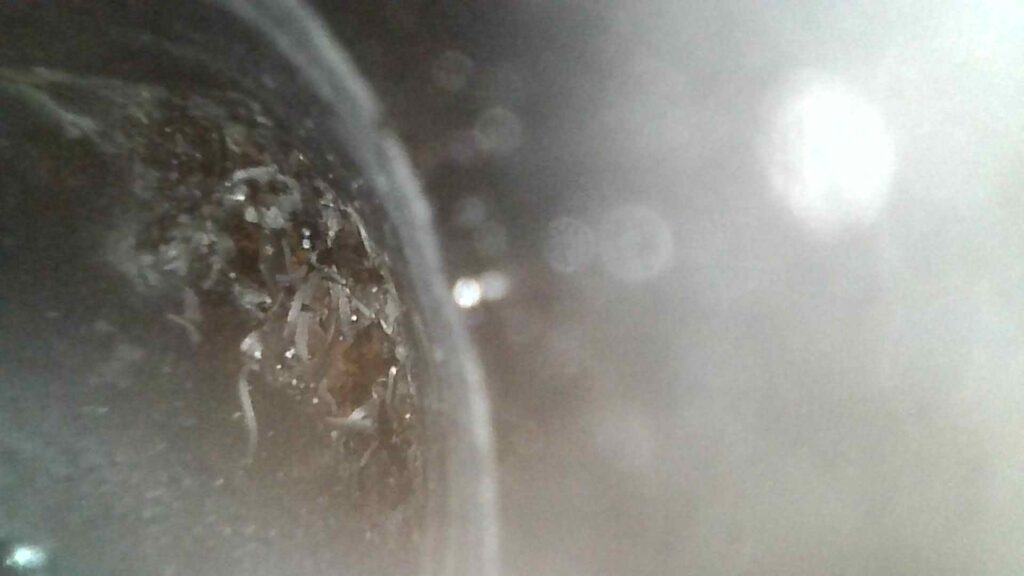
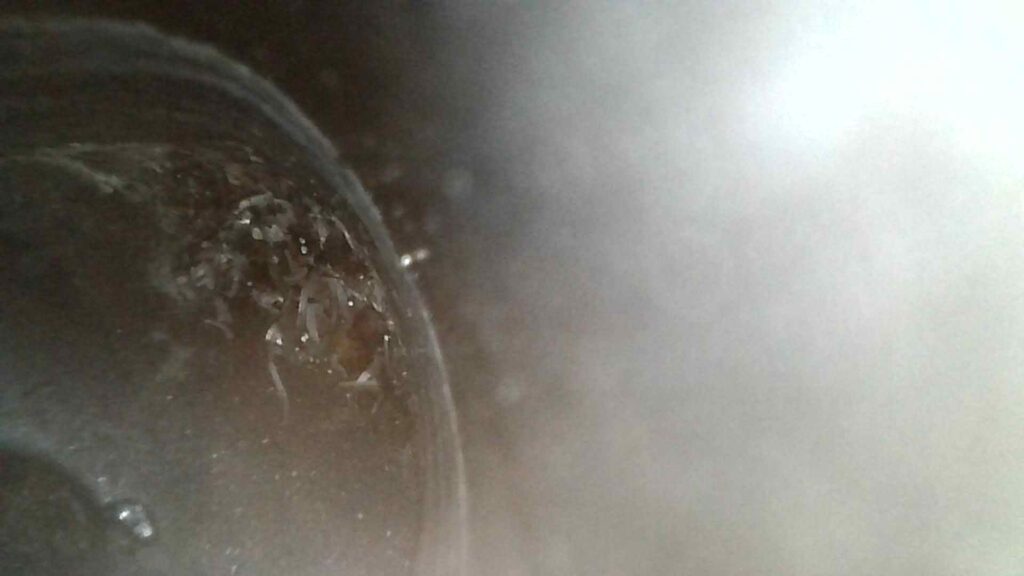
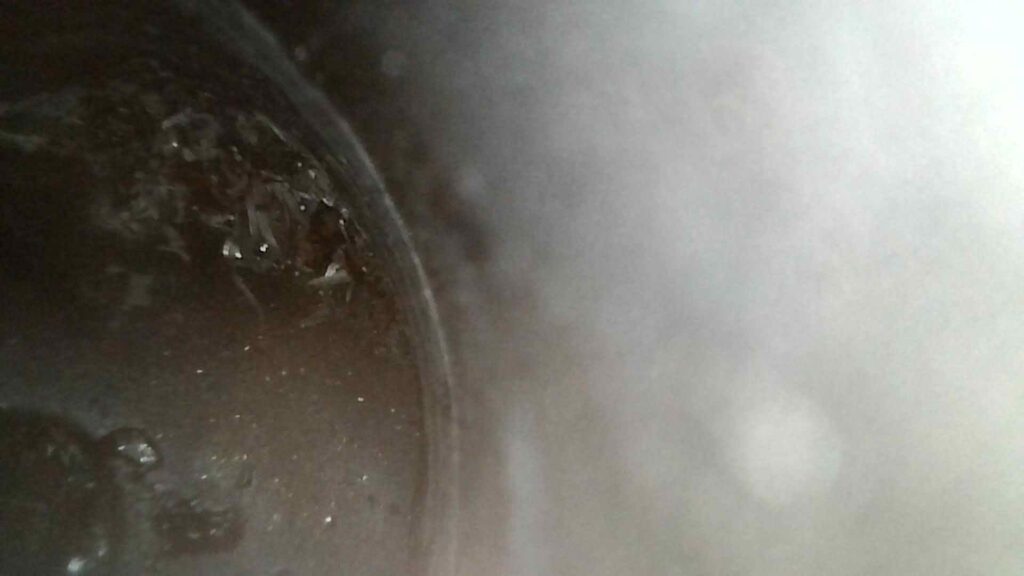
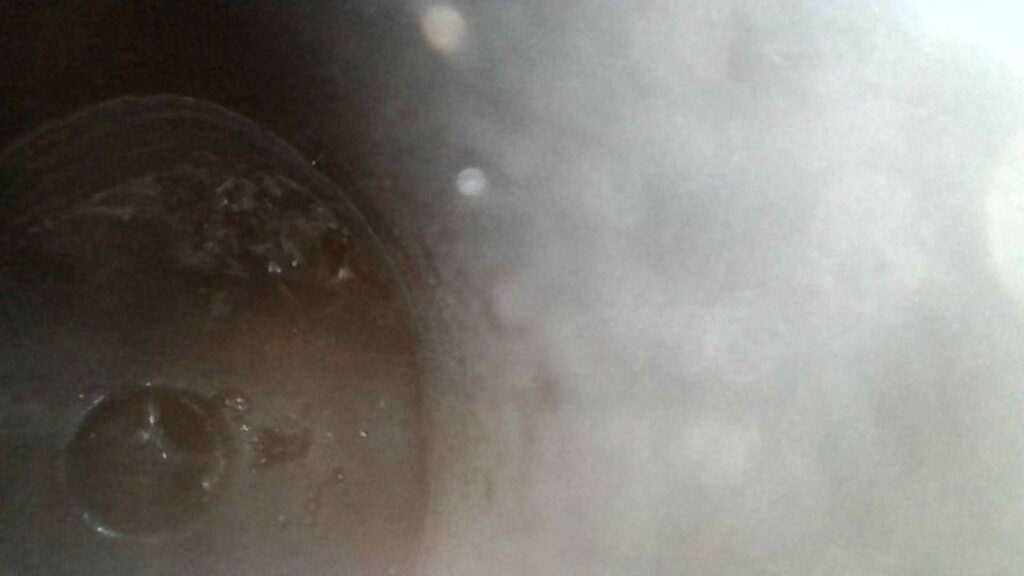
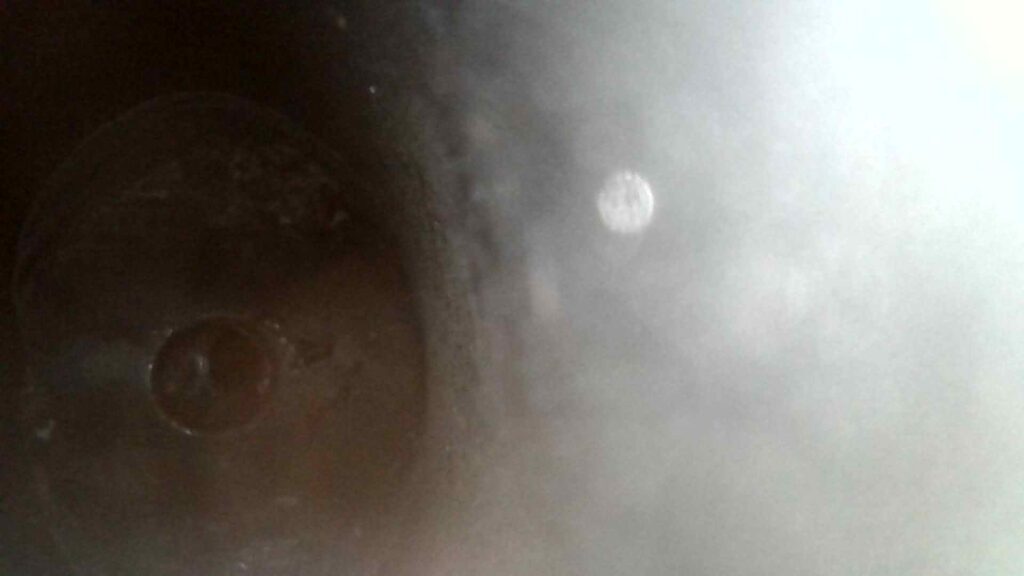
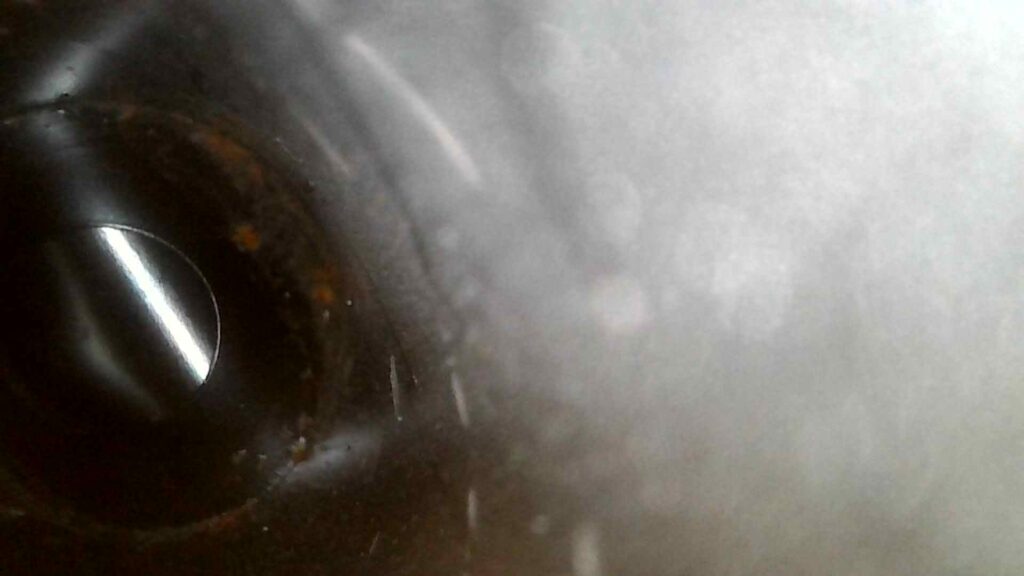
Response from the manufacturer – COTIC
The owner of the frame had viewed the analysis prior to public release and contacted Cotic for their response. It is pasted below verbatim.
Thanks for getting in touch. The corrosion he [Hambini] mentions is absolutely nothing to worry about, and the tubes are not a different material as he suggests. The surface corrosion is the mild steel used as the actual weld material, this is the case in every steel bicycle frame, and they all look like that inside. By all means pop something in there to stop it getting worse, but the whole frame has been dipped in an anti-corrosion zinc phosphate etch primer before being painted.
The only times we’ve ever seen corrosion on our frames to a serious extent, it has been through lack of care; ie large paint chips left unsealed and winter road grime not being washed off for several years. Corrosion from the outside, not beginning internally.
The holes are breather holes for the welding process, not drainage holes like he says. It’s also very light for such a tough frame, he clearly isn’t a mountain bike enthusiast.
I’m sure you’ll love riding the bike once it’s built up. There are plenty of 10+ year old Cotic frames still being enjoyed all over the world, all year round.
Cotic Bicycles
Hambini Media (ie the youtube channel) was copied onto the email from the customer, the response from Cotic explicitly excluded Hambini Media. The customer forwarded Cotic’s response out of courtesy.
Some contradictions were evident in Cotic’s response. They have claimed some of their holes, which are of small diameters <3mm are welding vent holes. Given their location, the engineering consensus was this was unlikely. Of concern was their response with regard to the corrosion. They claim the material of the frame was uniform and the frame had been dipped to prevent any corrosion. Given the seat tube was a large bore tube with plenty of access, it does not appear the claimed “zinc phosphate” anti-corrosion coating had made it to the weld filer during the dipping process.
Overall
The frame was found to be geometrically sound. The addition of waxoyl or an equivalent would probably be enough to arrest any potential corrosion problems internally. Their technical response with regard to the corrosion was somewhat dubious and suggests they are reselling this frame without total control of the manufacturing process.
wow, whatever “anti-corrosion zinc phosphate etch primer” must be pretty shit to let corrosion take hold that quick- it’s almost like it might not have been evenly applied
I would have thought that dipping would get to all of the cavities. But it doesn’t seem to have gotten through the seat tube opening