Ribble Cycles CGR AL – Multiple Failures of QA/QC and Technical Service
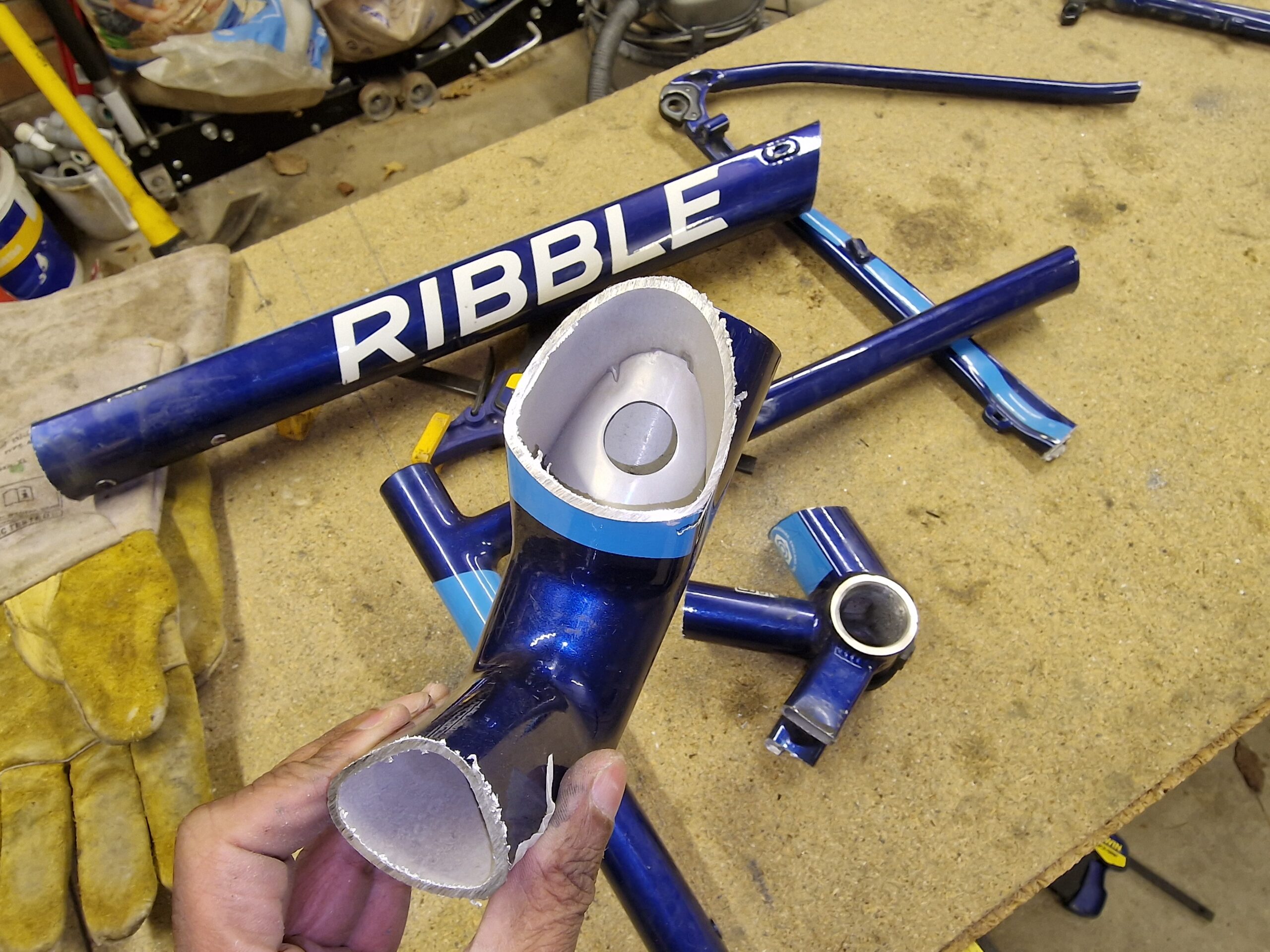
Introduction
Ribble cycles are a household name in the UK, they operate a large mail order business with over £10m turnover and several showrooms dotted around the country. They were also title sponsors of a cycling team and have a large social media presence including a supply of bikes to prominent YouTubers.
Ribble regularly runs deals through the UK media and is regularly featured in the deal catcher section of various UK-based publications.
Bike History
Recently, a Ribble CGR AL was sent into the channel by an unhappy viewer who had experienced numerous problems with the bike frame and Ribble’s service. In short, the bike was purchased from Ribble in 2019 and exhibited a creaking from the outset. Ribble attempted to remedy the fault twice, the viewer claimed on the first attempt an item was missing from the Bottom Bracket and on the second attempt they filled the bottom bracket with grease.
The bike was later taken to an independent bike shop where the mechanic showed the viewer that a simple splaying of the dropouts caused the creaking noise.
It was subsequently sent to Hambini HQ for analysis.
CGR Al Overview
The CGR AL is an aluminium bike made from 6000 series aluminium tubing. The frame has a combination of welded and brazed parts. The loaded rear end is predominantly welded. There has been some speculation as to whether the frame was robotically welded, given the level of compensation and intervention required in this particular frame, it is unlikely to have been robotically welded. The frame did not appear to be stress relieved.
The bike was purchased as a built unit and came equipped with a Shimano 105 drivetrain and hydraulic disc brakes. The headset is a standard preloaded double bearing unit that uses angular contact bearings for the upper bearing and lower bearing.
This bike is extremely popular, especially in the UK as it is well within the realms of the various bicycle to work tax incentive schemes that were pushed by the UK government.
The Creak
Upon receipt of the frame, an immediate attempt to recreate the creak was attempted. The noise was easy to repeat and only required flexing of the non-drive side rear triangle.
After a further detailed inspection, it was noted there was a small crack in the non-drive side seat stay, this was obscured by the letter R in the Ribble Logo. This crack corresponded to a flare in the stay and ran parallel to the chainstay. It is not totally clear if it was tooling damage, a clamp or the flare that caused the weak spot.
Further investigation showed a gross misalignment between the drive and non-drive side chainstays. The drive side chainstay appeared to be geometrically correct, the non-drive side stay showed signs of a gross correction at the weld area of the dropout.
Once the stays were cut a noticeable pinging as the inherent stress relieved itself was observed.
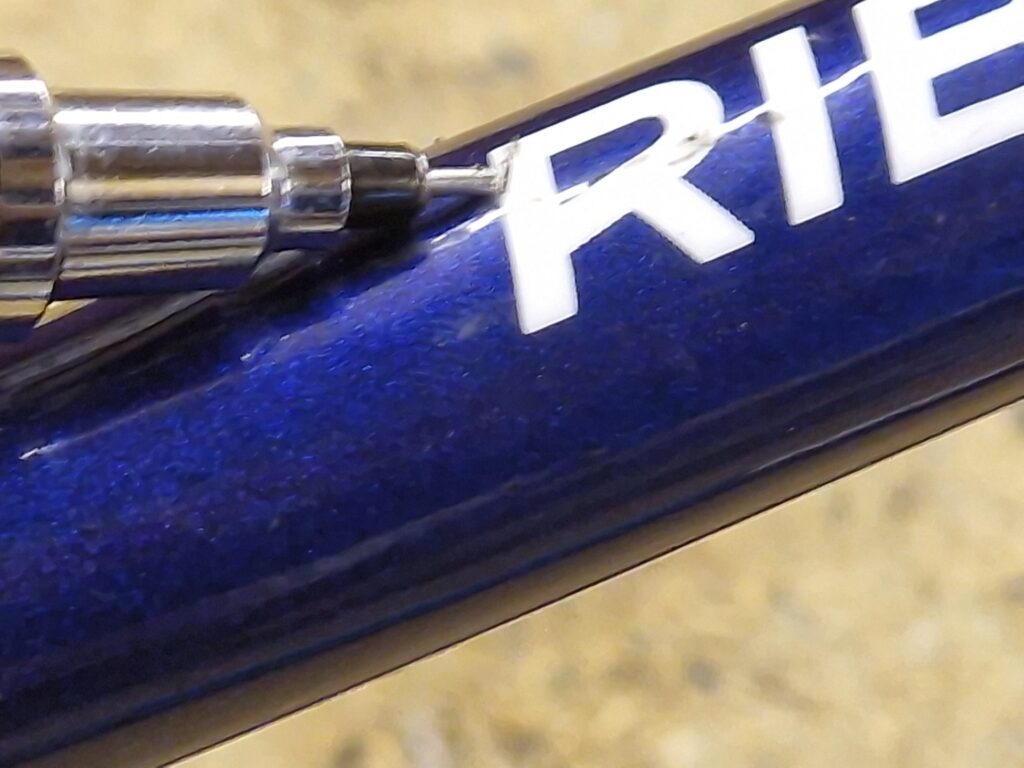
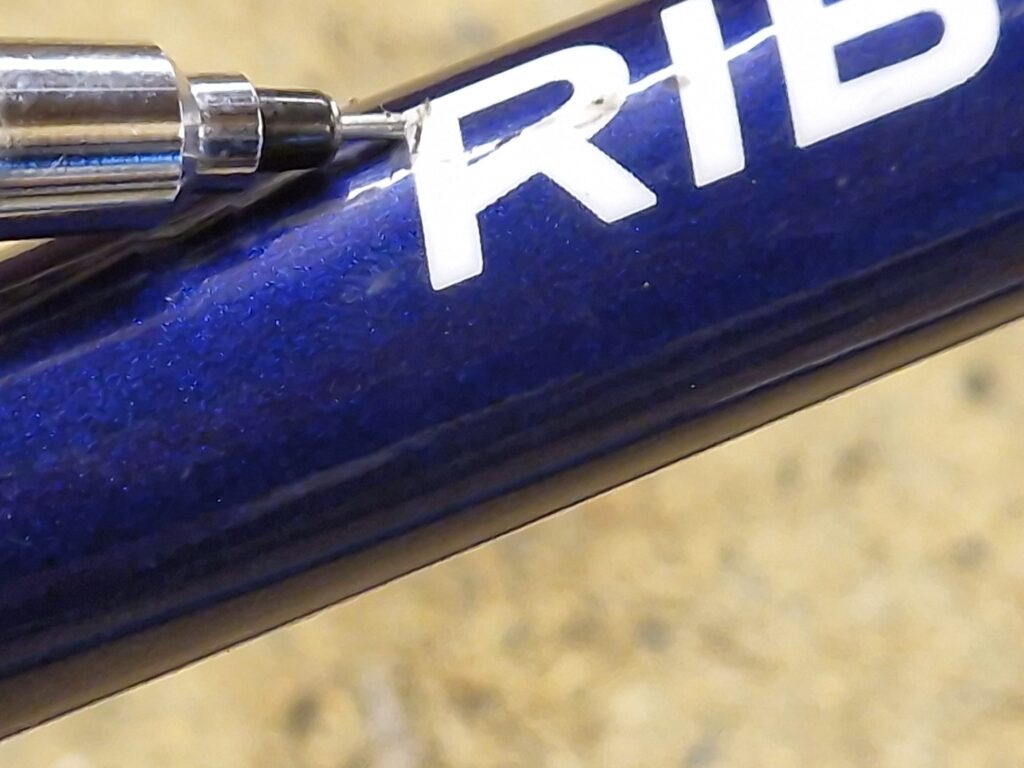
A contributing factor to the crack in either initiation or potential catastrophic failure was almost certainly the gross misalignment of the rear stay.
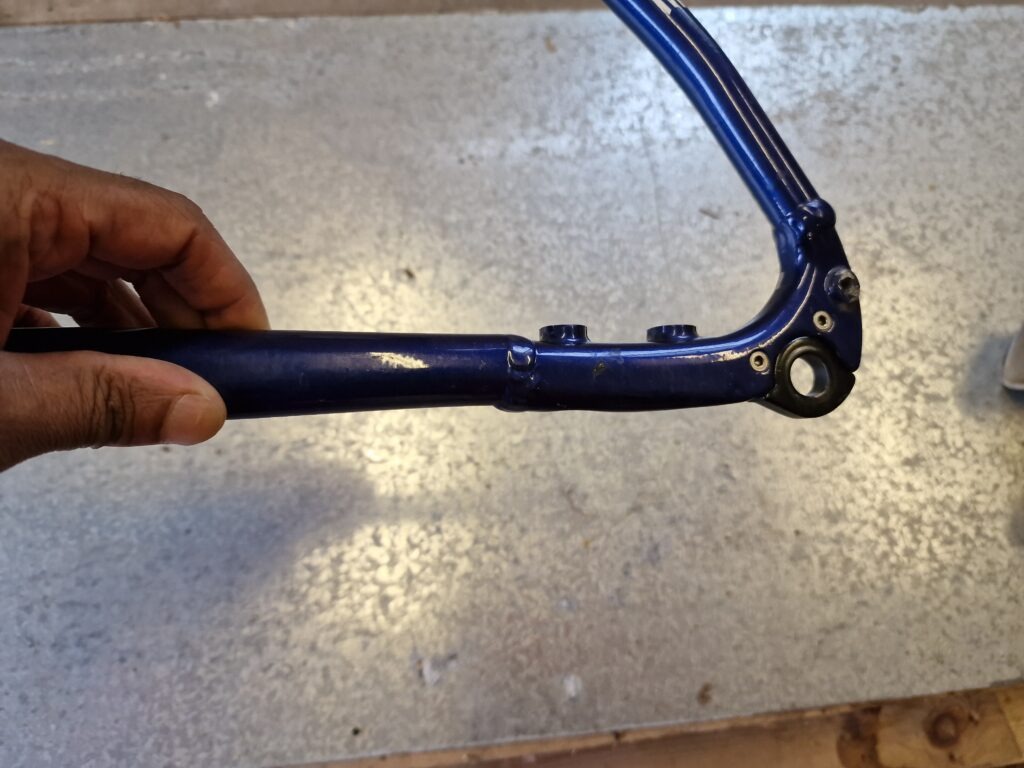
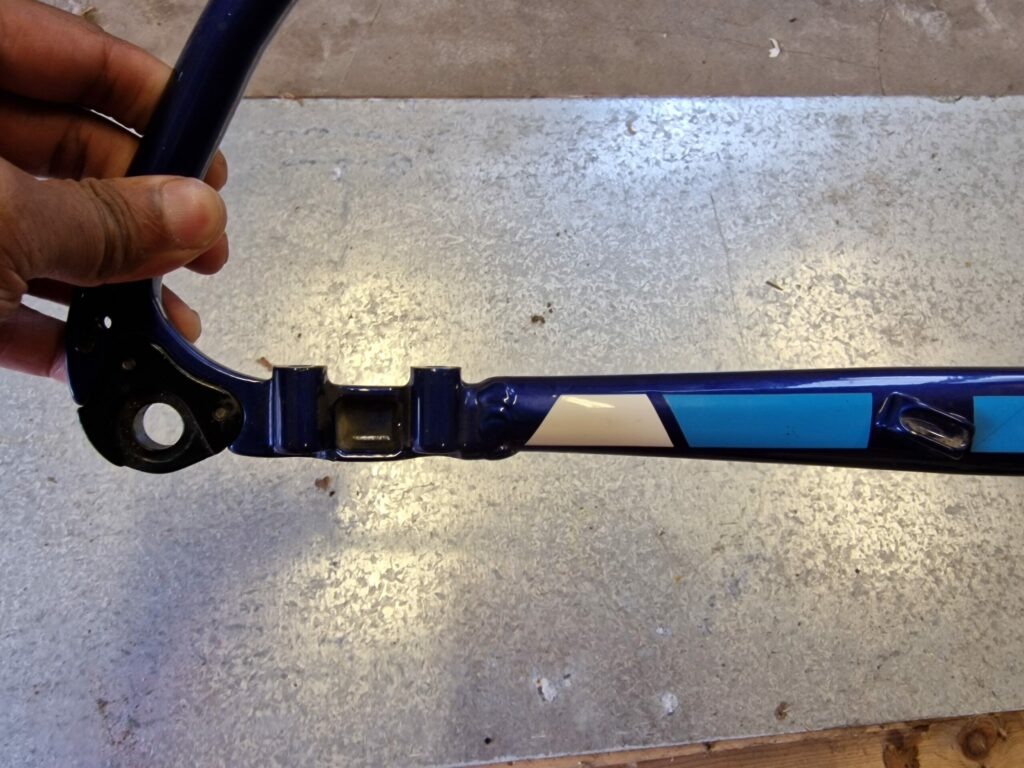
The gross misalignment can be seen once the stay has been sectioned. The upper part of the joint has been filled to compensate for the offset. The bottom of the stay joint has no gap and the bead is limited to the external periphery.
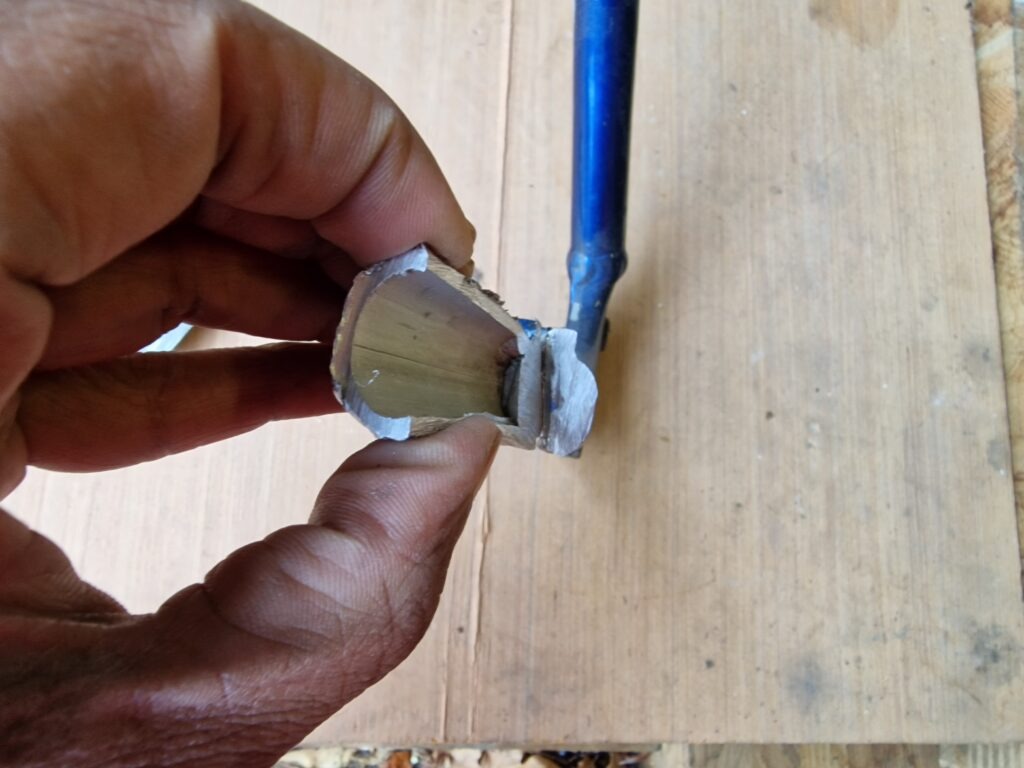
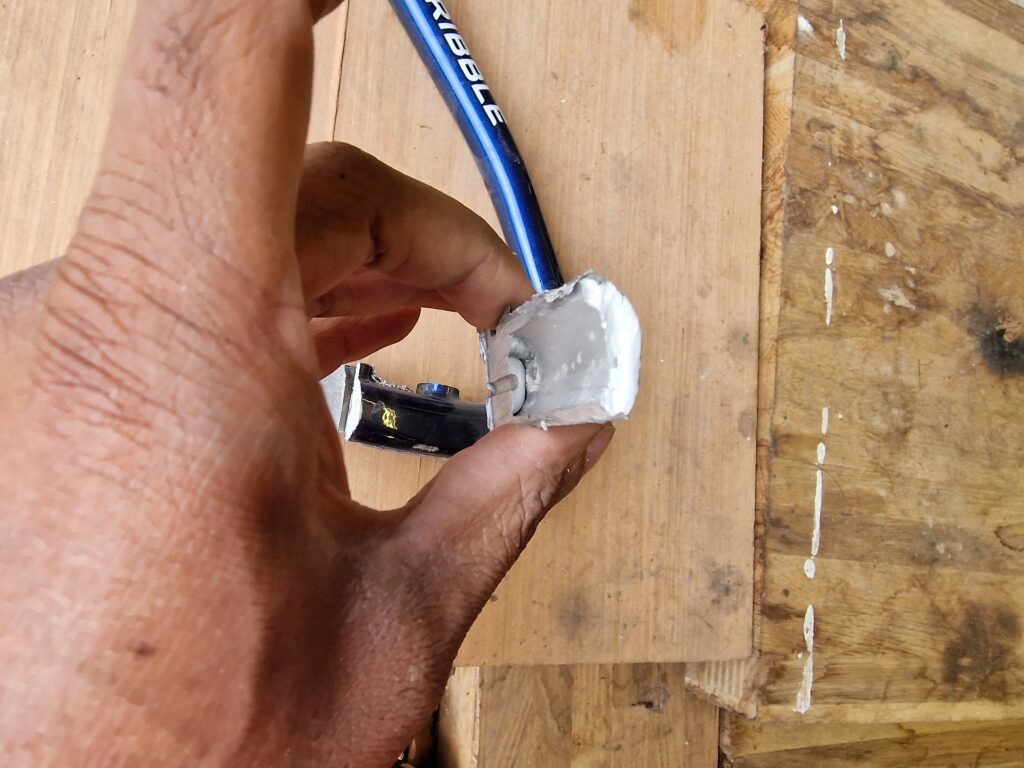
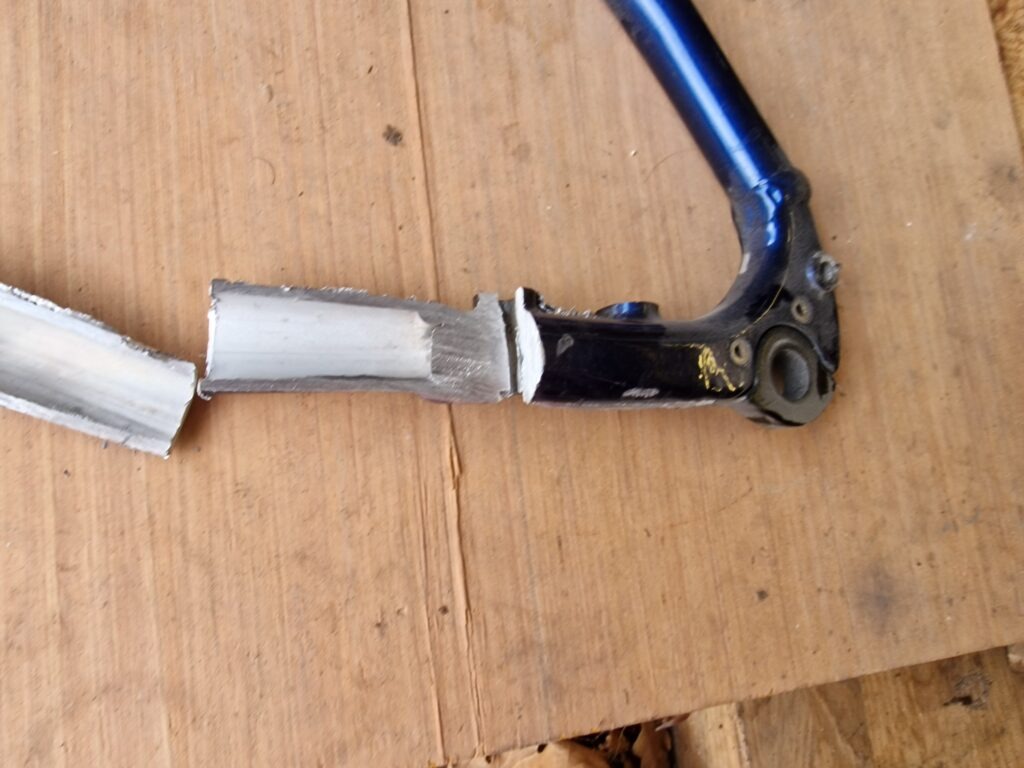
Lack of PEN?
The frame was probably built using a pre threaded bottom bracket and then subsequently welded. In an attempt to avoid distorting the frame and the geometry, the welding has very low penetration (or depth of fusion). The stays and the bottom bracket are considerably different thicknesses and this results in limited penetration into the bottom bracket. This was likely intentional. Conversely, there are signs of excessive heat in other areas where the weld has come through to the blind side.
A stronger and possibly more costly method would be to use deep penetration joints with subsequent post weld machining and stress relieving if required. This is by no means welding of the standard shown by Bowman Cycles
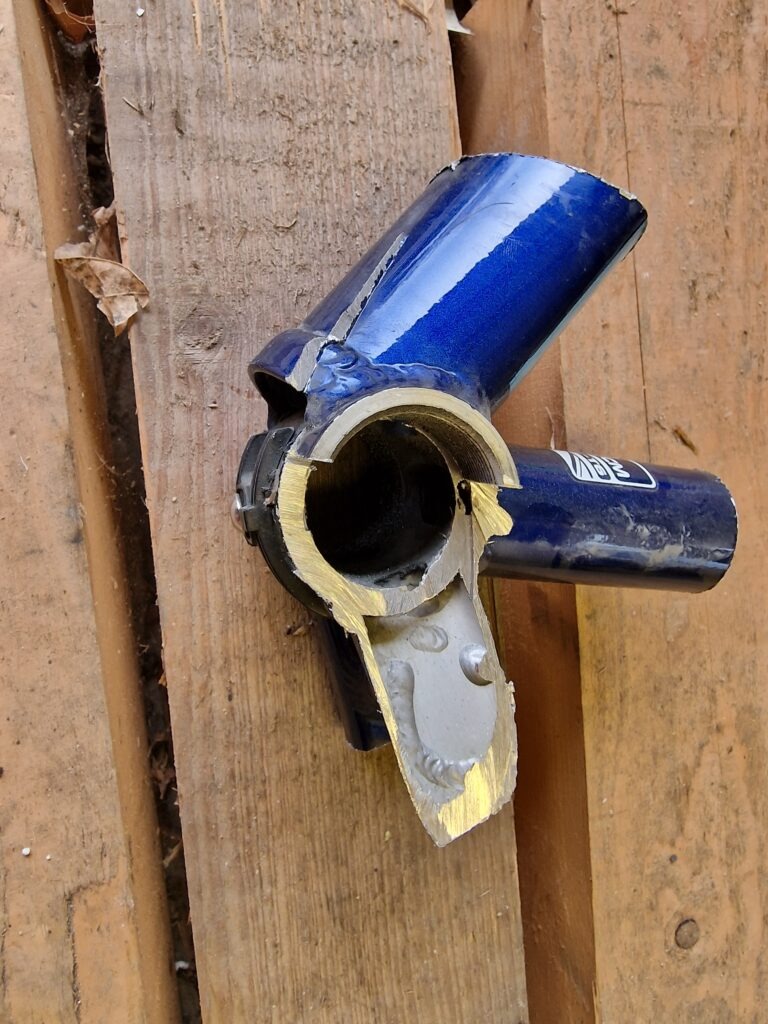
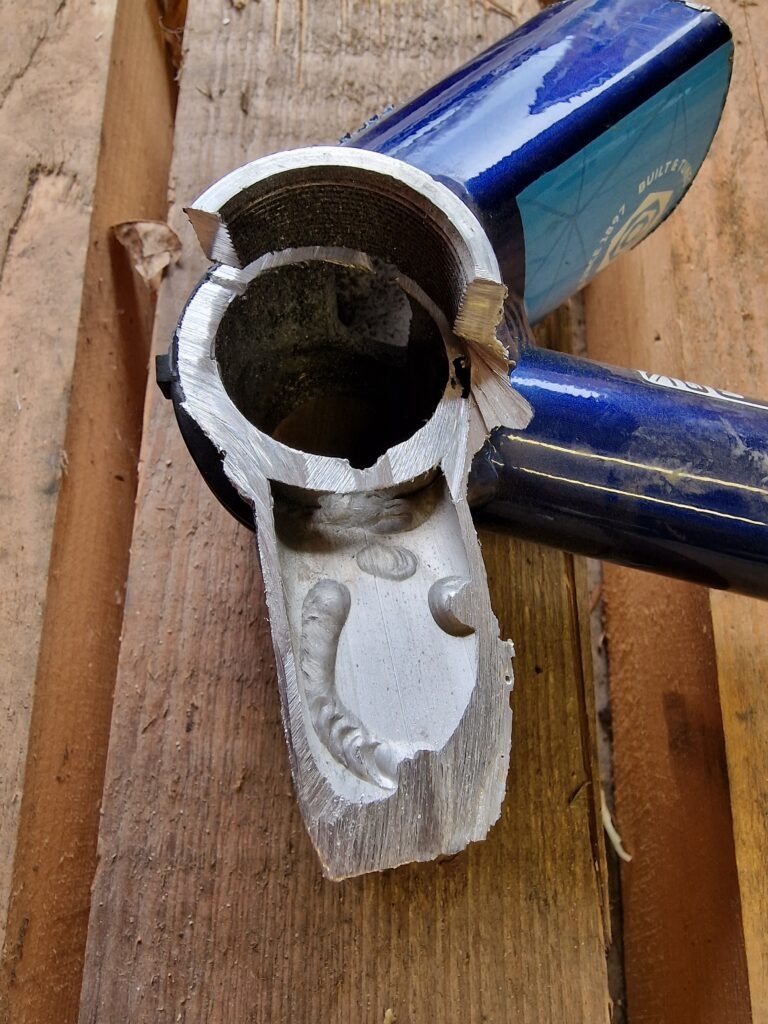
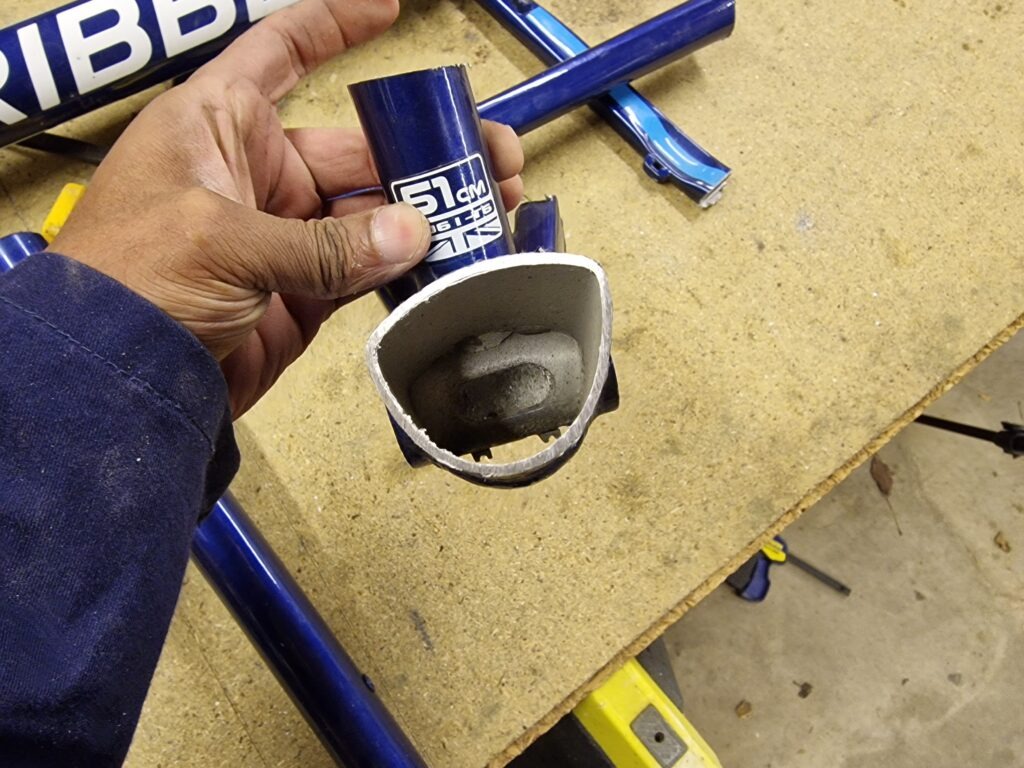
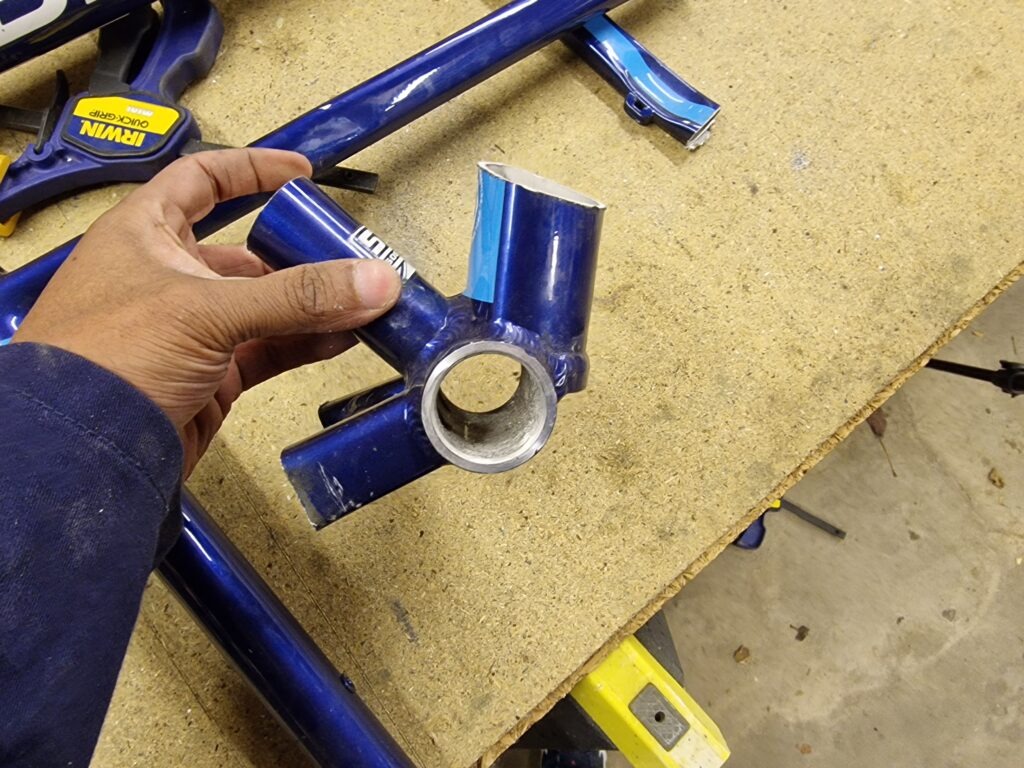
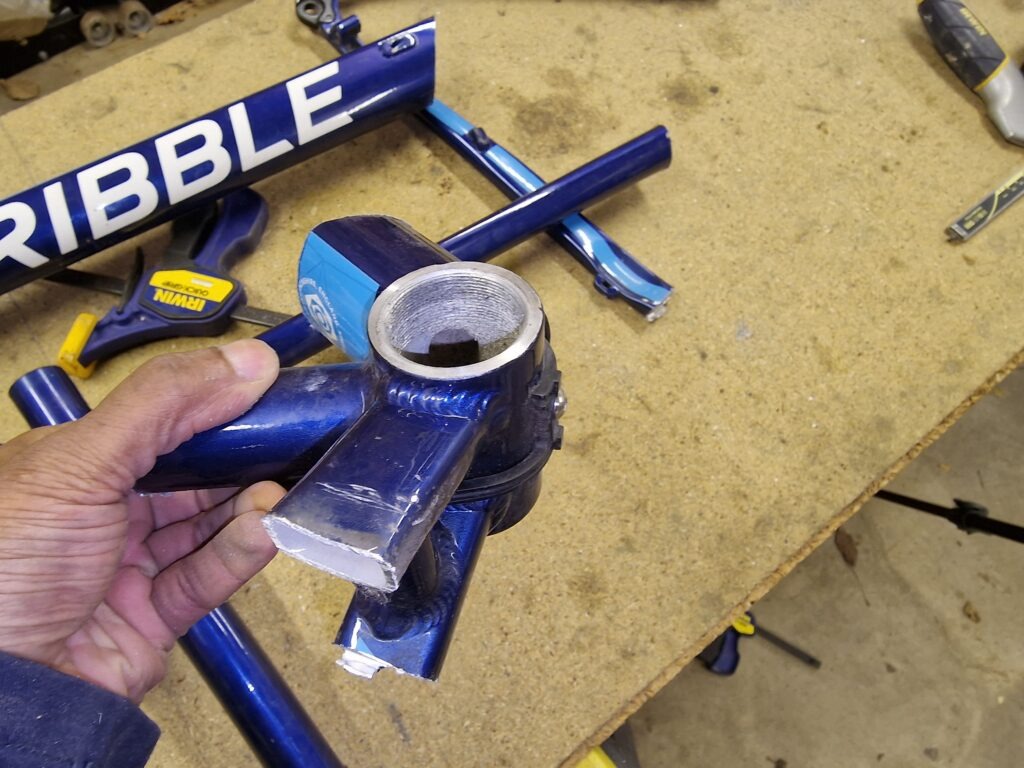
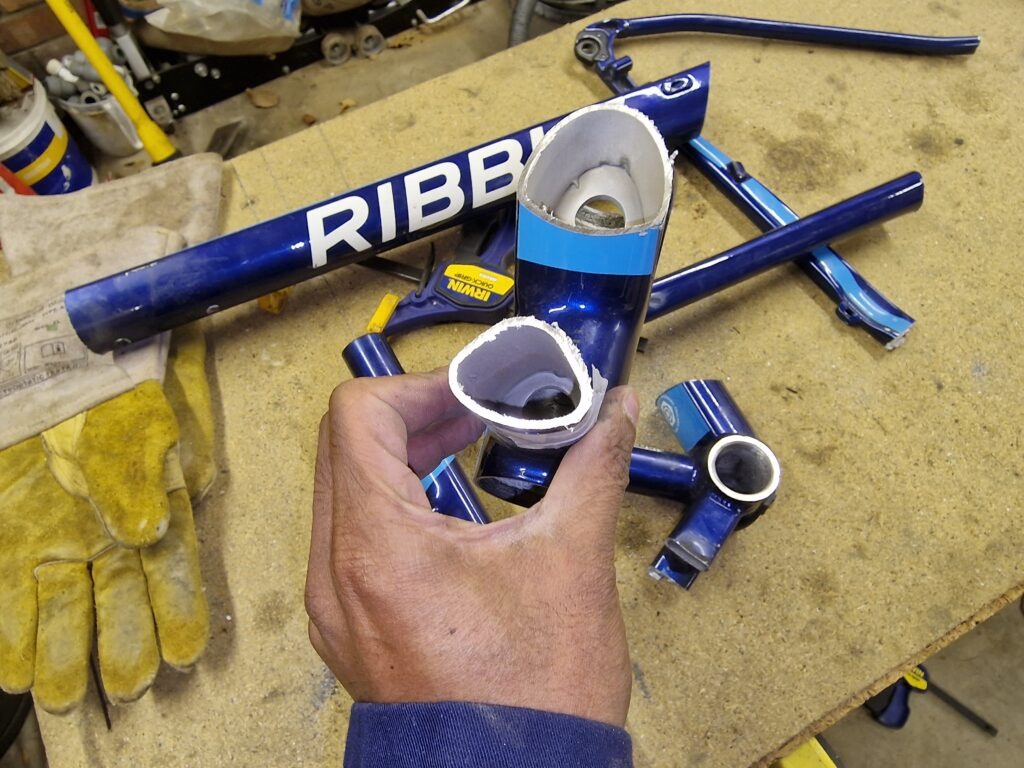
Multiple Failings
There are serious questions marks that have been raised by this episode. The most obvious is how a bike with this much of a geometrical fault was allowed to pass quality checks in welding, in despatch and build-up by Ribble. It would have been quite obvious that this frame would have been quite hard to insert or remove from a jig owing to the misalignment.
The bike was purchased as a built-up unit and the original building mechanic who (as Ribble claims) would have been in Preston, UK missed the fault.
The viewer claims he visited Ribble twice after purchasing for remedial action and the faults were not picked up on those occasions either.
Cracks are a precursor to a catastrophic failure without any prior warning.
The concern is the gravity of the fault. It is by no means a trivial fault and as a vendor, Ribble has a duty of care to ensure its products are fit for purpose. This bicycle should not have left the factory in such a condition, if the viewer’s testimony is found to be true and the alleged services did not pick it up. It would leave Ribble in a fairly precarious position as the viewer would have a strong case against Ribble for Negligence (both manufacture and supply of the bike and competent service after purchase).
Keeping them honest, great investigation and as always, love the entertainment
Thanks for the feedback!
Great info, thanks! I asked Handsling to send you a frame for review, don’t suppose they have been in touch?
No they haven’t i’m afraid
I would have loved to see the cracked area paint removed and it dye penned, to see how far the rabbit runs and crack formation and direction. Great findings and it hasn’t put me of buying from Ribble as they hopefully have learnt your lessons and have pulled their pants up and the Teflon welder has now been sacked or is now coded and experienced in the weld procedures. Also the frame jig has been adjusted and the QA has been given a kick up the arse.
Keep up the good work HPE.