Teardown: Campagnolo Ultra Torque Crankset Mechanics explained in Depth
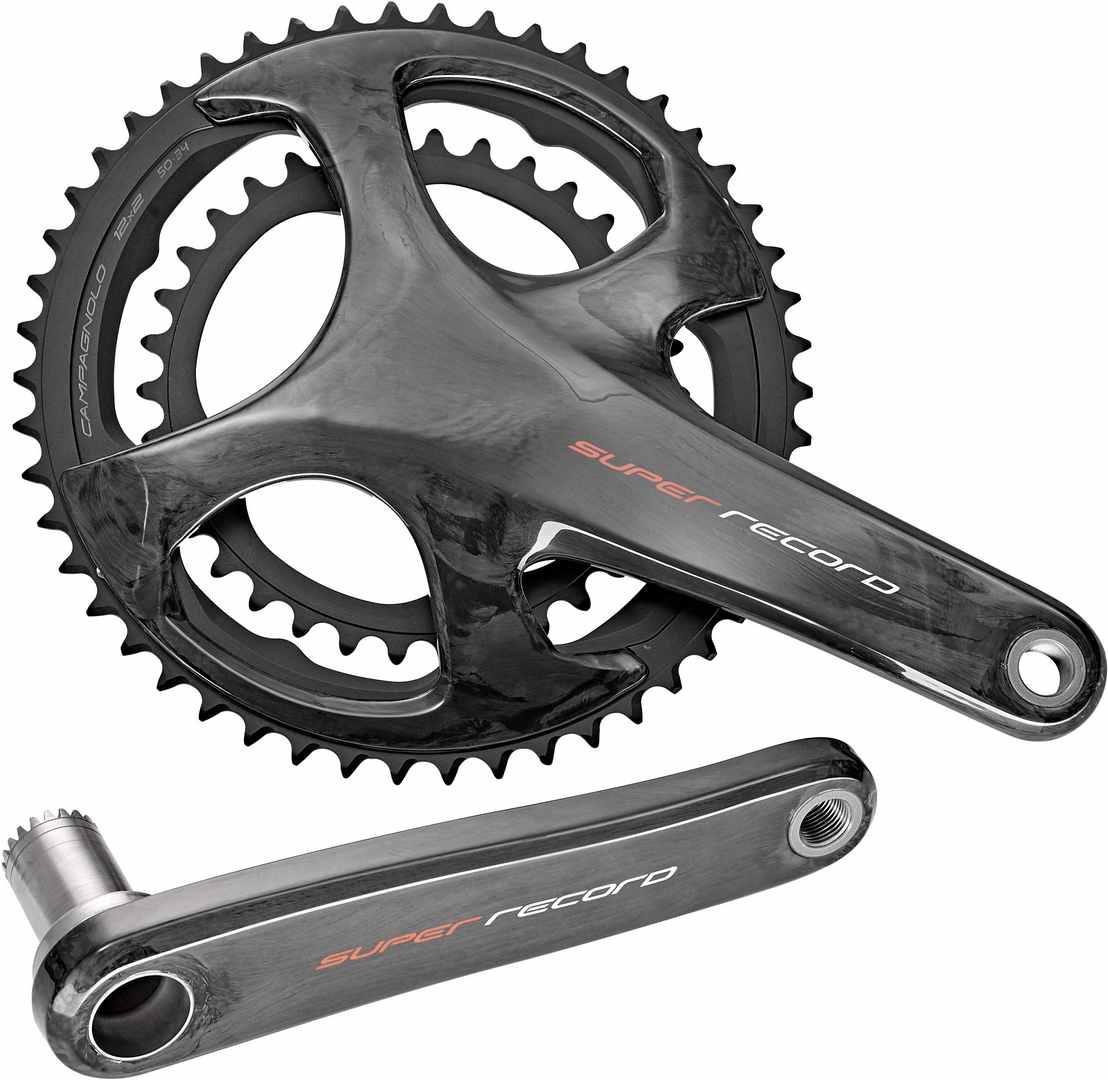
Introduction
Campagnolo cranksets have a reputation of being well engineered and robust but they are not without their problems and quirks. This post explains one of those in detail which surrounds the myths of the preload system, the “safety clip”, the system stiffness (or lack of it) and the involved nature of a bearing replacement. Campagnolo Ultra Torque is found on many of the upper range of Cranksets including the Super Record and Record.
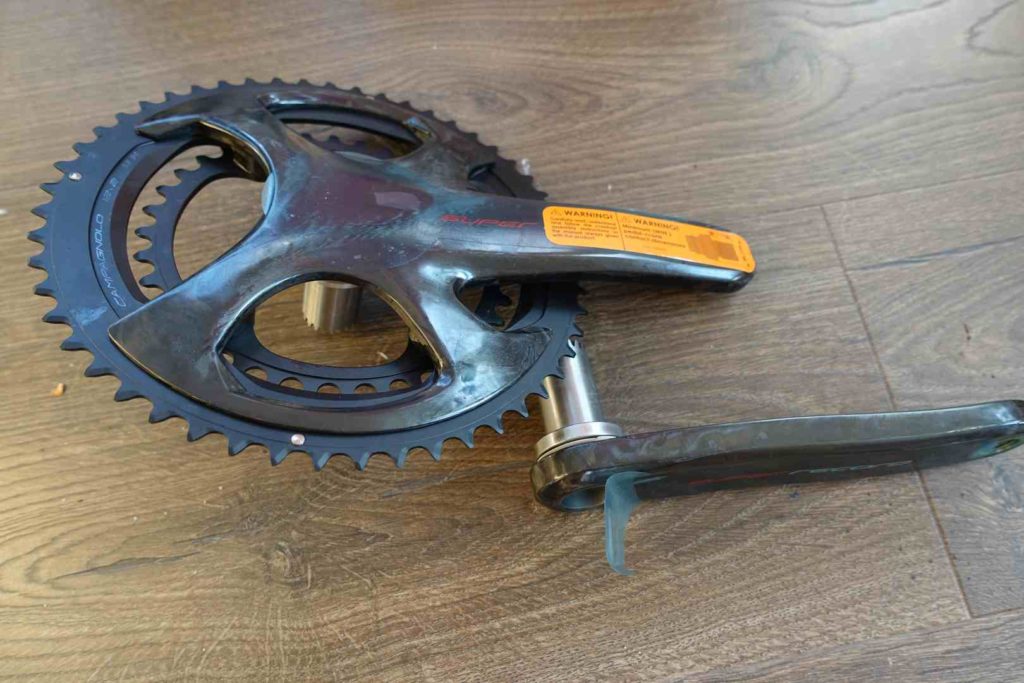
Basics
The Ultra torque system is one of the very few cranksets that use an interference fit on to the crank axle, the other notable mention is Look’s BB65 which uses one bearing with a shaft interference. This has many advantages from a manufacturing perspective because this fit is easy to control – it’s a machined fit from a lathe as opposed to a molded fit on a bike frame. Shaft interference is also much less likely to creak because the roundness can be closely controlled, unlike housing interference which is much more of a lottery.
The system consists of two halves of the crankset with a hirth joint in the middle. Hirth joints are inherent much less stiff than a solid axle. Hirth joints are commonly used in Aerospace applications as the interface between drive components, those components tend to be fairly lightweight and have low torque but spin at high speed (10,000RPM+). This is very different to the typical bike crank axle. A technical paper on the stiffness of hirth couplings versus solid axles can be found here. The key point from that paper is regarding loading factor. Under large torque, the axle will not behave like a solid axle because of the discontinuity created by the joint. Bicycle cranks create a problem because the torque is cyclical in nature.
The machining of a hirth joint is by no means an easy task and is one of the reasons why the crankset is expensive to manufacture. The retention forces involved in Hirth Joints are large, hence a comparatively large bolt torque of ~50Nm is required to secure the two halves of the axle and the axle must be made from a suitably hard material. Titanium or steel are obvious choices.
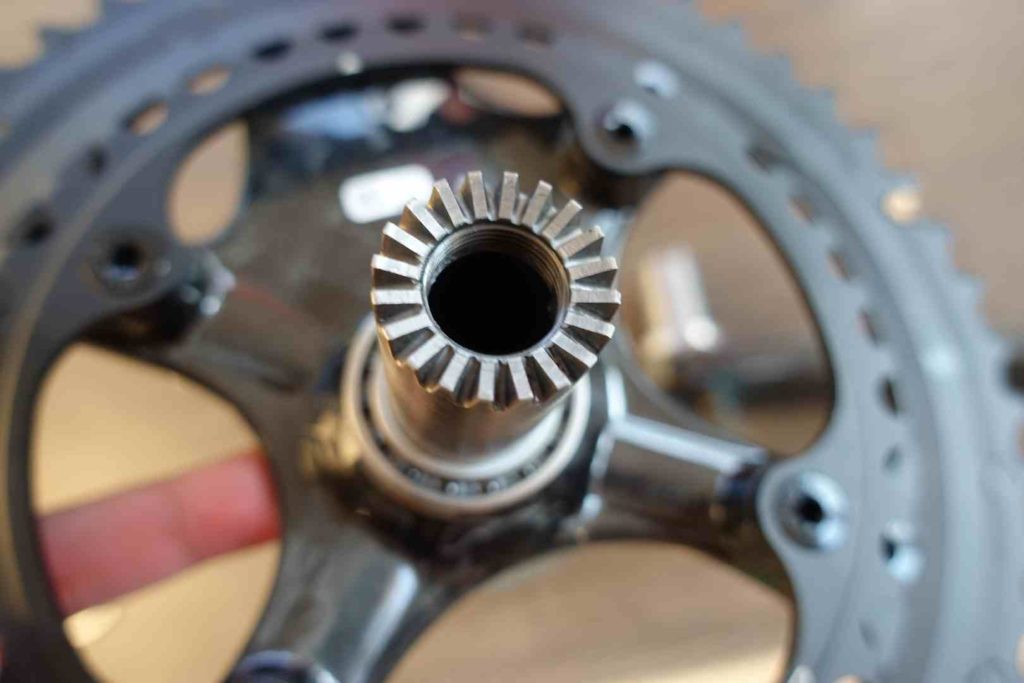
Bearing Choice
On higher end Campagnolo cranks, the bearings are FAG cronitect (CULT), these bearings use ceramic balls combined with hardened steel races. The bearings are classed as hybrid bearings, the inner raceways are hardened whilst the outers are comparatively soft. They do not have any external seals. On one side the bearing is completely open. On the other side, the cage forms part of the seal (albeit a poor one and Campagnolo have installed a secondary seal). The manufacturer (Schaeffler Group) previously developed this technology for use in the food industry.
Campagnolo could have chosen to go with standard 6805 bearings but out of choice they elected to fit 6805N bearings which have a much narrower width – 6mm versus 7mm. This does allow the center of the bearing to be placed further outboard but this does mean that the user will have to pay $140 for a bearing replacement when they do fail.
The lower end cranks have sealed bearings.
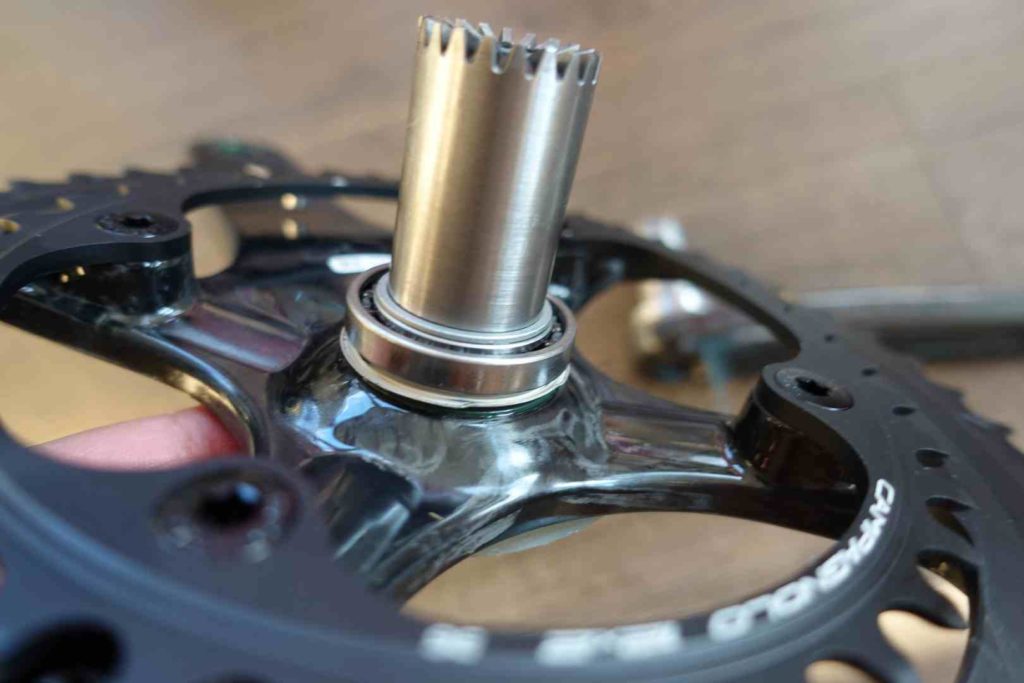
Whilst a bearing replacement on a crank system which has housing interference generally involves a punch and a mallet, a bearing replacement on Campagnolo ultra torque requires a specialized gear puller that is prohibitively expensive and takes the job away from the home mechanic and moves it towards the bike shop.
Bearings of any type work on the principle of hertzian contact. A frictionless contact between two bodies. The underlying basic principle is to minimize the contact area between two bodies to a point where it is infinitesimally small (theoretically generating an infinite stress). In reality there is a bit of deformation at the contact point between surfaces. Ceramic bearings rely on their hardness to take this principle to the extreme – they minimize the deformation due to their high hardness and thus minimal deformation. This principle works providing the two materials are of a similar hardness. Prior to FAG Cronitect there was always a huge disparity between the hardness of the balls and the races.
Poor Machining Quality
The photographs below show the Campagnolo Super Record as of 2021, the manufacturing quality is quite poor. There are no reliefs on the axle and the entire length is of the same ground diameter. This makes the installation require constant force from the hirth joint down towards the bearing seat. Most other manufacturers relieve the axle and only have the ground finish at the bearing landings. Whilst this is not show stopper it does indicate some of the “hidden” cost saving that has been employed on this product.
The Preload System in detail
One of the biggest misconceptions of Campagnolo Ultra torque is the use of the retaining clip. The primary function of this device is to prevent lateral play in the bearing assembly and adopts a “fixed” drive side to “floating” non drive side bearing arrangement. This type of arrangement is common in industrial machinery such as blowers and pumps but does not lend itself well to applications that have alternating axial loads.
In the case of the Campagnolo system, the theorized and actual have a few key differences. The most obvious is the use of the retaining clip. It is designed to securely hold the drive side bearing in a fixed position. In reality, there is a small clearance between the clip prongs and the bearing. 2 point pin retention on the bearing is not considered good practice and a fixed collar or minimum of 4 point retention is considered superior. It should be pointed out that despite this, very few pin failures have been documented.
A system performance issue that is overlooked is the flexibility of the clips. They are regarded at a system level to be infinitely stiff but the reality is they have a high degree of flexibility and under load they will bend.
Additionally, many people have reported play between the clip and the bearing, typically this is 0.25mm – 1.00mm of unwanted end float. This could be shimmed out but this is problematic as machining thin shims tends to make them dish and they are rarely flat due to residual internal stresses.
The diagram below shows a schematic view of Campagnolo Ultra torque. The top half shows the idealized system and the bottom half shows the “as manufactured”. The two key elements for discussion are the pin and the preload adjustment (wave washer)
The preload is governed by the amount of axial force generated by the system. That load is derived from two factors, the first is the spring constant of the wave washer and the second is the amount of compression. The spring constant typically varies by +/-10% (this increases to 15% for wave washers), this is due to the material properties of spring steel being inconsistent. The amount of compression is directly related to the width of the bike frame. Campagnolo stipulate a maximum frame tolerance range of 1mm whilst the industry typically quotes 2mm. 2mm is a range that the current crop of cranksets from Rotor, Shimano and SRAM can comfortably deal with.
A huge drawback in ceramic bearing operation is the reliance on preload. Two bodies which are extremely hard and extremely smooth tend towards a frictionless ideology and thus require large amounts of preload to avoid the surfaces sliding as opposed to rotating. An analogy would be to have a bike on a turbo trainer with a perfectly smooth tire made of a hard material such as steel driving a turbo trainer roller which is equally smooth and equally hard. It would require much more tension on the roller to get it to spin than the same setup with a wheel made of a softer material that deformed. The rider would generally find the wheel would slip (slide) and the rate of ultimate power transfer would be diminished. The concept of traction and weight over certain axles in motor vehicles is analogous to this. The weight is essentially the preload.
By virtue of the left and right load application of the pedaling action, the axial load going through a bottom bracket constantly changes direction. Additionally, a high degree of stiffness is desired as it’s the primary load input point. SKF, NTN and even FAG explicitly state the use of a wave washer in this application is not recommended. SKF explicitly state
The (spring) method is not suitable for bearing applications where a high degree of stiffness is required, where the direction of axial load changes, or where undefined peak loads can occur.
SKF
For optimum preloading to occur, it is WIDELY accepted that the preload must EXCEED the maximum axial force generated in the opposing direction. This is to keep the balls spinning on the active side of the bearing. A movement of the axle to load the non active side is detrimental in both stiffness and in this case drag. If this practice was adopted in Campagnolo Ultra torque, the wave washer would require preloading to the point it was almost flat, it would negate the requirement for the “safety clip”. The clip exists because the tolerance of the wave washer and bike frames cannot be controlled accurately enough to limit the axial movement. In many cases the pin is impacted by bearing movement and this causes fretting. The bottom bracket cups are made of aluminium which is a very soft metal, the pin in contrast is hardened steel. This combination of material differential hardness exacerbates the problem.
One key parameter that many cyclists believe governs stiffness are the crank arms and only the crank arms. Carbon crank arms being the flavour of the month. The reality is very different, stiffness will always be limited by the stiffness of the most flexible element. In this case, a likely combination of the wave washer and possibly the hirth coupling.
Drive and Non Drive side Float
Another misconception is the idea of chainline and float. Lots of users (mainly on internet forums) believe the drive side bearing must be fixed and that all “float” must be on the non drive side. This is poor guidance. Fixed and floating positions can only be governed if items are allowed to move. If the bearing schematic diagram was flipped over, the maximum float which is governed by the pin clearance and the wave washer would remain the same (labelled as 0.25 -1.00 TYP) the only difference would be the DIRECTION of the float. In the above case, the crank would move away from the centreline of the bike, if it was flipped it would move towards the centreline of the bike.
It is not advantageous to have the fixed bearing move from the active side to the non active side of the bearing race. This causes friction and the transient movement.
Both SKF and ironically FAG recommend sufficient compression is applied to the wave washer such that the retaining safety pin is negated by having a restraining force that exceeds the maximum axial load applied by pedaling. By doing this, the limit is the remaining travel in the preload wave washer and not the pin clearance. This avoids the active and non active sides of the bearing races becoming reversed during pedaling. In this scenario the lateral movement is low and is such that the position of the wave washer is completely irrelevant.
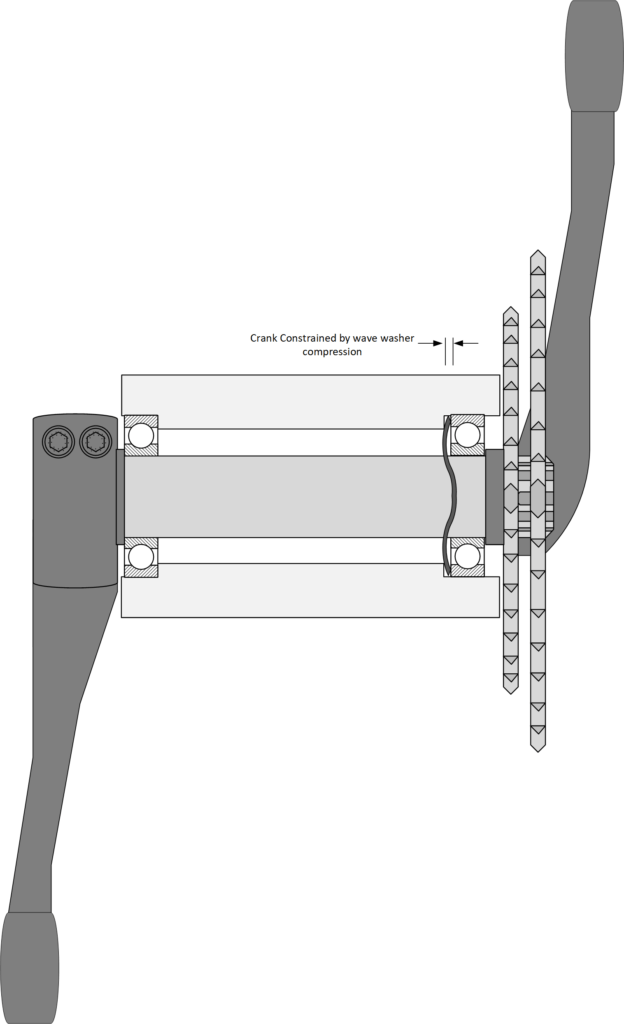
There is considerable variation in the spring constant of campagnolo wave washers. The Campagnolo Technical leader (Velotech, Graeme Freestone King) for the UK stated the variation was around +/-10%. When measured the range was found to be +/- 20%, a total range of 40%. It’s likely that many users will be relying on the safety pin to constrain the crank with this level of movement – although given the pin fretting highlighted above, they are probably unaware of it.
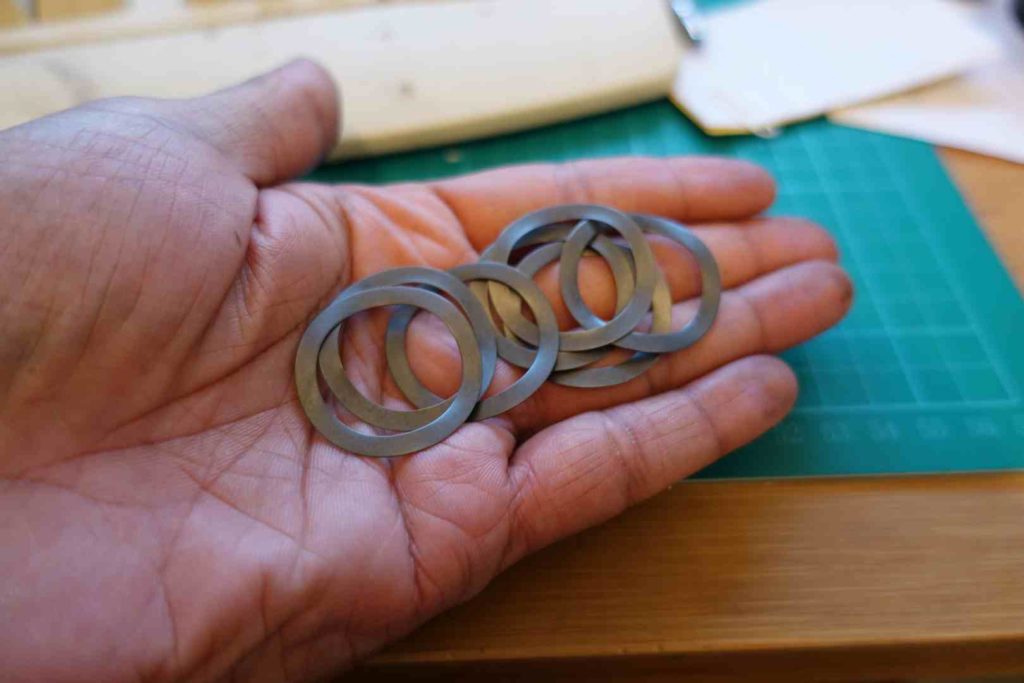
Conclusion
Campagnolo has a hardened user base that uses their products and generally “swears” by them. Issues arise because the service of Campagnolo is beyond the scope of most home mechanics. The quality of machining on the reviewed crankset is quite poor and lots of cost cutting has been carried out. Given the crankset is one of the most expensive available this is slightly concerning.
The bearing arrangement of Campagnolo is by no means optimized, it may work but the transfer of load from active to non active bearing race side is undesirable from a purely mechanical perspective – a fact echoed by the OEM of the bearings. The bearing arrangement is also quite poor for ultimate stiffness.
The use of a hirth coupling is required to facilitate this quirky bearing setup, that creates a crank axle that is around 40-50% less stiff than an equivalent Shimano Axle because of material discontinuities.
There are plenty of cyclists who simply say it just works. That might be the case but it is by no means as good as they perhaps think. For technical superiority, the Look BB65 is the stiffest albeit that comes with it’s own issues regarding compatibility.
https://blog.fairwheelbikes.com/reviews-and-testing/road-bike-crank-testing/
Campagnolo UT:
Deflection-D: 4.1 mm
Deflection-ND: 6.9 mm
Average Deflection: 5.5 mm
S/W: 2.680
Dura-Ace HT2
Deflection-D: 3.98 mm
Deflection-ND: 7.67 mm
Average Deflection: 5.83 mm
S/W: 2.46
+ The CULT bearing (Cronitect) is corrosion-resistant and far best in cycling world.
The testing in the link you’ve highlighted does not take into account the stiffness lost through the bearing arrangement. That will be far more than the crank deflection if any. Whilst the CULT bearing is regarded as the pinnacle of ceramic, it is probably no better than the considerably cheaper NTN offering that comes with full seals and is a doddle to install.
“if any”, “probably”?
Bearing arrangement of Campagnolo UT is better (wider) than Shimano HT2. The CULT bearing (Cronitect) is corrosion-resistant so it isn’t need full seals and grease (maybe some synthetic oil). The J&L Bearing Puller and Installation Tool for UT are about 30 USD on ebay… I use NTN 6806 LLB too (for 30mm axle), but the CULT Cronitec is far better, than anything other. What is considerably cheaper? A pair of CULT bearing (£89.99) or many lower grade, slightly cheaper…
Corrosion isn’t the only problem a bearing faces. A major issue is contamination. Water introduces fine sand and other particles into the bearings. These grind down the bearing surfaces, sometimes very quick.
2019’s Liege-Bastogne-Liege sportif ruining 1 pair of cult bearings within one day for me. I checked and greased the bearing in the days before. Then came 8 hours of riding in rain. Afterwards both bearings had a mixture of sand and water within them and developed so much play, you could pick the outer race from the inner by hand.
Yes, “if any” and “probably”.
Because once in application, designs will never behave exactly as theorized. That’s why there’s prototypes.
Just as seen in your example of bearing choice: in impeccable conditions, they are unmatched. But conditions are rarely impeccable, aren’t they?
Specialized S-Works crank also has hirth joint and similar issues. S-Works has the bearing pressed into the frame and an external wave washer. But the problem of torque and non axial load is the same. Same clunking especially when riding out of the saddle on steep climbs. As the bike gets old and wears, the tolerance gaps are greater and the issue becomes apparent. Adding spacers and/or wave washers can help. But in the end I just got sick of noise and trying to fix it. Shimano HollowTech crank has fixed the issue.
Hambini, I’m sure you defined the terms active and non-active side in some video. Would you mind, explaining once again?
Hello Hambini, could it be a solution to shim the bb-caps to the perfect width, where the wave washer has the right pressure (shims between caps an frame)? It only works with threaded caps of course.
yes you could do that with no issues.
Additional question: If I use one or two regular 6805 bearings, I could get rid of the wave washer and the restraining clip at all. The 1-2 additional mm bearing thickness would fill the room where the wave washer was before. Am I right? I would adjust the preload by shimming the bb-caps. I know, I would need very thin shims, but that´s a different question.
This idea would lead to a very simple but effictive solution for the campy-system. They should just make the NDS BB-Cup adjustable with a lockring like it was with earlier loose ball bottom brackets.
Sorry for bothering with these questions, but I am looking for a good/improved bsa crankset and I can´t stand an Ultegra/DuraAce crank with my Campy group.
Best regards
Holger
I wasn’t the first one with this idea. There is a long Story from Roguemechanic about this topic (check his Youtube Channel). He sells a complete shim kit incl. Installation video. https://www.mavicparts.com/products/roguemechanic-shim-kit-for-campagnolo-ultra-torque
You’d have to be very lucky to get the preload right, by shimming only. The shims would have to be impractically thin to allow for that. Chances are you apply too much or too little preload.
If you apply to little preload the system continues to have play, which leads to what Hambini described above.
If the spacer is too thick you end up with c***loads of preload, which will lead to premature wear, very premature wear.
As soon as you have wear, the system will become loose again, and you end up with too little preload, thus a different type of wear, as descried above.
You will just be shimming forever and gain very little.
I would be interested to find what the differences are between the Ultra Torque and Campagnolo’s Power Torque. The Power Torque doesn’t use the Hirth Joint and it uses standard 6805 bearings not the 6805N. And the wave washer acts against the inner race of the bearing and not the outer race as in the Ultra Torque.
The power torque is a lot more like the sram and BB30 systems where the axle floats inside the bearings. It would probably need a fair amount of analysis to figure out the actual ins and outs.
I’ve owned both PT and UT cranks, wearing out one PT crankset (2015 centaur) and one UT bearing. The PT axle failed where the crankarm mounts to the axle on the splines, the splines themselves got worn away and caused play of the crankarm. This took about 5 years with about 3-6000km of cycling a year in all weather conditions.
The UT bearing (left side) got shredded by dirt, salt & water after about 1500km of winter riding, due to its open/unsealed nature. Fairly easy to replace, this was on a Chorus 12 crankset and I think this comes with steel bearings rather than the more expensive CULT bearings.
Side note, the PT bearings comes installed in one of the cups and one on the spindle (on crankset axle).
My cranks don’t have a pin, I have them PF30 into a 386 frame with FSA adaptor cups. But one thing that’s not clear in your article, despite discussing it at length, is whether you advise the wavy washer to be on the drive side or non-drive side, or whether it makes no difference in a standard installation – and whether as a consequence you agree or disagree with the campagnolo assertion that wavy washer goes on the NDS. Please, if you could clarify that in no more than a sentence or two that’d be informative. Thanks
Thanks for the video. Most of it is way too technical for me, but I think I understand now why the bearings on the Chorus cranks – which I’ve just had taken out of an Aspéro frame – and had only done kms 3000 kms (albeit all on dirt, some of which was quite corrugated) were noticeably corroded. I can see now why Campagnolo are using different bearing cups on the Ekar groupset, but wonder how much difference it will actually make.
Hello amazing article and video ! Is your thread fit BB bracket for Campagnolo still available for purchase?
Came across this while searching for bearing removal tool. Three years later it would be interesting to know what these engineering shortcomings mean in real life. Any statistics regarding failures/malfunctioning? Personally I have done tens of thousands of kilometers with my original ultra torque crankset. No noise no play, never taken apart, never changed the bearings so far. Of course I hardly put out any watts and only ride in dry weather, but still…